Abstract
Purpose
This study aims to improve the availability of regenerative braking for urban metro vehicles by introducing a sensorless operational temperature estimation method for the braking resistor (BR) onboard the vehicle, which overcomes the vulnerability of having conventional temperature sensor.
Design/methodology/approach
In this study, the energy model based sensorless estimation method is developed. By analyzing the structure and the convection dissipation process of the BR onboard the vehicle, the energy-based operational temperature model of the BR and its cooling domain is established. By adopting Newton's law of cooling and the law of conservation of energy, the energy and temperature dynamic of the BR can be stated. To minimize the use of all kinds of sensors (including both thermal and electrical), a novel regenerative braking power calculation method is proposed, which involves only the voltage of DC traction network and the duty cycle of the chopping circuit; both of them are available for the traction control unit (TCU) of the vehicle. By utilizing a real-time iterative calculation and updating the parameter of the energy model, the operational temperature of the BR can be obtained and monitored in a sensorless manner.
Findings
In this study, a sensorless estimation/monitoring method of the operational temperature of BR is proposed. The results show that it is possible to utilize the existing electrical sensors that is mandatory for the traction unit’s operation to estimate the operational temperature of BR, instead of adding dedicated thermal sensors. The results also validate the effectiveness of the proposal is acceptable for the engineering practical.
Originality/value
The proposal of this study provides novel concepts for the sensorless operational temperature monitoring of BR onboard rolling stocks. The proposed method only involves quasi-global electrical variable and the internal control signal within the TCU.
Keywords
Citation
Zhao, L., Liu, K., Liu, D. and Jin, Z. (2023), "Energy model based sensorless estimation method for operational temperature of braking resistor onboard metro vehicles", Railway Sciences, Vol. 2 No. 4, pp. 470-485. https://doi.org/10.1108/RS-10-2023-0031
Publisher
:Emerald Publishing Limited
Copyright © 2023, Leiting Zhao, Kan Liu, Donghui Liu and Zheming Jin
License
Published in Railway Sciences. Published by Emerald Publishing Limited. This article is published under the Creative Commons Attribution (CC BY 4.0) licence. Anyone may reproduce, distribute, translate and create derivative works of this article (for both commercial and non-commercial purposes), subject to full attribution to the original publication and authors. The full terms of this licence may be seen at http://creativecommons.org/licences/by/4.0/legalcode
1. Introduction and literature review
With the rapid development of the world economy, urban populations and per capita motor vehicle ownership have sharply increased. High-capacity metro transit plays an increasingly prominent role in optimizing urban space structures and alleviating congestion in modern large and medium-sized cities' public transportation systems. Among these, the subway, as a vital tool in metro transit, is gaining favor rapidly in plenty of cities due to its advantages such as high passenger capacity, less travelling times, safety guarantee, energy efficiency and avoid traditional vehicle traffic disruptions.
To minimize the loss of braking shoes, regenerative braking, as known as electric braking, is widely used in all kinds of rolling stocks, especially for the underground metro vehicles. The regenerative braking is to make the electrical machines that powers the vehicle to work as generators, thus, absorbing the kinetic energy of the vehicle to deaccelerate and to brake. For now, the proportion of regenerative braking used in metro vehicles is still continuously increasing, some of the newly built vehicles are required to be able to daily operate with only regenerative braking (with conventional mechanical braking for emergency). Yet, the regenerative braking results in a reverse power flow, and this power need to be consumed or dissipated. However, during the operation of metro vehicles, traction substations typically use uncontrolled rectification to provide power, and stable DC power grid or energy feedback system are not widely equipped by metro operating company due to its construction and maintenance cost, as a result, the DC network is lack of energy absorption capacity. To address this, ground breaking resistors, ground flywheel energy storage devices or regenerative braking devices are often installed along the railway to absorb the regenerative energy generated when vehicles are in regenerative braking mode. Furthermore, when the ground absorption devices experience a short-term malfunction or fail to absorb all the braking energy generated by vehicles on the line, the DC voltage in the power grid would rise, causing an abnormal increase in the DC voltage on the traction inverter's DC side. Additionally, factors such as changes in overhead catenary current conditions, sudden load variations and DC side oscillations in the traction inverter can also lead to an abnormal increase in the DC voltage exceeding its overvoltage protection limit, resulting in the locking of the traction system and the loss of traction or braking capability for the vehicle. To prevent frequent locking of the traction inverter due to overvoltage conditions, a chopper bridge arm is typically installed between the positive and negative buses of the intermediate DC circuit in the traction inverter as shown in Figure 1. This chopper bridge arm consists of IGBT modules and braking resistors in series. When the intermediate DC voltage exceeds a threshold, the regenerative braking IGBT modules are triggered, dissipating energy in the BR to keep the DC voltage within the normal operating range, allowing the traction inverter to continue functioning correctly.
As the BR dissipates the regenerative power in the form of heat, the frequent braking of metro’s daily operation will result in severe temperature rising of the BR, which may lead to damage to the BR bank itself (Liu, 2018), overvoltage of the DC traction network (Li, & Zhang, 2005), unavailability of regenerative braking. All of these will be an obvious risk to the vehicle’s safety as well as to the system’s security. Therefore, the temperature monitoring of the BR is mandatory for the metro vehicle.
Currently, the study of BR bank’s temperature dynamic focuses on the thermal design and the thermal dynamic of the BR bank, including the maximum temperature rise under extreme conditions (Wang, 2019; Lee, Kang, & Shim, 2015), optimization of heat transfer coefficient (Neale, Derome, Blocken, & Carmeliet, 2007), optimization of heatsink and cooling structure (Sun et al., 2015a, b), etc. In Gao et al., 2021, the differential equations of simplified thermal dynamic of a BR bank are established, in which the Newton's law of cooling is introduced. In Hu, Qin, Zhu, Peng, and Wang (2021, October), the author propose to measure the energy that dissipated by the BR and chopper, yet, the results clearly shows that the loss in the chopper circuit is not comparable to the huge energy dissipation in the BR. In Liu, Shi, and Wu (2002), the temperature rises of an electric locomotive’s BR bank is quantitatively calculated by adopting the law of energy conservation, yet, in this study the regenerative power is measured using multiple sensors. In Lee, Shim, and Hyun (2013), the transient temperature rises of a BR bank is calculated by adopting lumped parameters and it considers the influence of thermal radiation in the calculation process, yet, judging by the results, it also indicates that the impact of thermal radiation is not so obvious. For these studies, the temperature rise and the thermal dynamic are mainly done in an offline manner. To ensure the safety of daily operation, the real-time temperature monitoring or estimation is needed.
The conventional methodology of the temperature monitoring of the BR’s transient temperature is to use temperature sensor. Yet, the temperature sensor is relatively vulnerable in the harsh operational environment of metro vehicle, especially when it is compared to the BR bank itself. Thus, a large amount of the alerts is caused by the temperature sensor, instead of the BR overheating. The false alert will consequently lead unavailability of regenerative braking and loss in the braking shoe. Moreover, the traditional temperature sensor has inherent delay effects, which are particularly problematic in conditions where component temperatures change rapidly during an extremely short period. Furthermore, braking resistors typically carry high currents when overloaded. If insulation damage occurs, there is a high probability of causing damage to the control system through the wiring between the temperature sensor and the controller. For these reasons, the sensorless temperature monitoring methodology is needed.
In this paper, an energy model-based method is proposed and developed to conduct real-time temperature estimation in a sensorless manner. The energy model of the BR bank is established with consideration of input power/heat dynamic, convection dissipation of heat and the impact of temperature rise on BR material/resistance. The major input of the model is intentionally selected to be the voltage of the DC traction network and the duty cycle of the chopper circuit that controls the operation of the BR bank. It is noteworthy that the voltage of the DC traction network is a quasi-global electrical variable to the metro vehicle, which means the voltage can be measured by each voltage sensor in each TCU and, thus, minimizing the vulnerability from the presence of all kinds of sensor. In this way, the proposal utilizes only the electrical sensor that is necessary for the electric drive system and the internal control signal of the chopper circuit to achieve the real-time temperature estimation in the process of iterative calculation and updating the parameter of the energy model, which opens a new way to achieve sensorless operational temperature monitoring of the BR onboard metro vehicles.
2. The energy model of the BR bank
2.1 Dissipation of the BR bank
As shown in Figure 2, a typical BR bank is mainly composed of a sealing of the BR bank (i.e. the box), a number of braking resistor units, the built-in cooling air duct and a cooling fan. For metro vehicles, the BR banks are composed of several braking resistor units placed in parallel (in horizontal direction), and each braking resistor unit is composed of multiple parallel resistor pieces (in vertical direction). Some pressure ribs are installed into the parallel resistor pieces which can enhance ventilation, heat dissipation and reduce their thermal deformation. For metro vehicles, the station-to-station distance is relatively short, thus, the cooling of the BR bank is mostly done by the forced-air cooling method, which is also selected as the benchmark study case of this work.
In case of using BR to limit the voltage of the DC traction network, the regenerative power will be converted into heat. The high temperature of heated resistor pieces drives thermal energy exchange with the cooling air, which causes heat conduction, heat convection and heat radiation during the process. Among them, the heat convection is the major driving force of the cooling process, according to the calculation, around 94% of the heat is dissipated by this process.
The movement of cooling air at the surface of the BR can be illustrated as shown in Figure 3. As shown in Figure 2, the built-in cooling air duct can be considered as a parallel tunnel, where the resistor pieces are located. The cooling air absorbs the thermal energy at the surface of the resistor pieces, and, thus, resulting in a change to its own temperature and flow velocity. For this reason, the thermal temperature of different brake resistor unit will be naturally be different, the heat spot will be at the last unit.
2.2 The energy model of the BR bank
To study the temperature dynamic of the BR bank, an energy model is established using controlled element method.
2.2.1 Controlled volume temperature model for energy dissipation
As the vertical movement of the cooling air in the same resistor unit can be considered to be similar, their difference in temperature dynamic can be neglected, thus, only one of the resistor pieces is studied for each resistor unit in this work. To simplify the calculation and to avoid solving complex temperature distribution, according to the Biot number criterion, the temperature of the studied resistor element is considered to be uniform, and the originally continuously distributed mass and heat capacity are concentrated at one point. Therefore, the entire BR bank can be equivalent to a layer of resistive pieces along the cooling-air-flow’s direction, and the temperature of each single resistive pieces is consistent. Considering the actual needs of the engineering practice, this study selects the layer located in the central area of the air duct, that is, the section with the highest temperature, for discussion.
To study the thermal dynamic of the resistor pieces, the area contains the resistor piece and the part of the fluid domain near its location is considered as a control volume, as illustrated in Figure 4.
The volume of the controlled volume is presented by:
v – The velocity of the cooling-air flow;
S – The area of the cooling duct;
dt – The time interval;
In addition, the temperature dynamic is considered to change during the process, as denoted in Figure 4.where Tin – The inlet temperature of the cooling air.
Tout – The outlet temperature of the cooling air;
ρk – The density of the cooling air;
ck – The specific heat capacity of cooling air;
Tkn – The temperature of the cooling air at time interval n (present);
Tkn-1 – The temperature of the cooling air at time interval n-1(last moment);
For each of the resistor piece, its temperature will obey the law of conservation of energy. The thermal effect of the current will cause the resistor to heat up, and its heat production can be presented by:
Pbr – The electrical power consumed by the resistor;
According to the Newton's law of cooling, due to the energy exchange by the process of heat convection, the heat absorbed by the cooling air can be presented by:
h – The heat transfer coefficient of the convective;
A – The area of the resistor’s surface;
Tdn – The temperature of the resistor’s surface;
Tkn – The temperature of the cooling air;
The resistor piece’s temperature will change during the process, and it’s dynamic shall follow:
cd – The specific heat capacity of resistor material;
Vd – The volume of the resistor piece;
dTdn – The temperature change during the process (in unity time interval);
According to the law of conservation of energy, the energy of the controlled volume shall follow:
By assuming the initial temperature at n-th time interval (i.e. present) of the resistor piece to be Tdn-1, by substitute (2), (3) and (4) into (5), the internal energy of the resistor piece can be presented by:
Such a first-order non-homogeneous linear differential equation can be solved with its initial condition. The solution of (6) can be presented by:
Equation (7) gives a solution to the temperature change, by substitute (7) into (3), the energy exchange of the cooling air and the resistor can be presented by:
The cooling air within the controlled volume will also obey the law of conservation of energy, that is to say, during the time interval dt, the internal energy change of the air shall be expressed by:
As the outlet air is the air flow that leaves the controlled volume, that is to say Tout = Tkn. By substitute this into (9), the equation can be deformed into:
By substitute (8) into (10), the air temperature within the controlled volume can be further presented by:
By adopting (7) and (11), the energy dissipation process can be described and calculated.
2.2.2 Surface temperature of the resistors
Due to the fact that the exchanged energy by heat convection is affected by the temperature of cooling air, thus, the thermal dynamic indicated by (7) and (11) shall be utilized to calculate the surface temperature of each resistor units.
By selecting the i-th (i = 1∼6) controlled volume, according to (7), the surface temperature of the i-th resistor unit can be presented by:
It is noteworthy that the cooling air flows through the resistor units one by one, that is to say the inlet air of the i-th controlled volume is the outlet air of the (i-1)-th controlled volume. For this reason, the air temperature of the i-th controlled volume shall be presented by:
By adopting (12) and (13), the temperature of each resistor unit can be iteratively solved, the instantaneous temperature of the entire braking resistor can be obtained. Such process can be utilized as an algorithm, the flow chart of which can be presented as shown in Figure 5.
2.3 Input power of energy model using sensorless estimation
In a state-of-the-art traction system of metro vehicle is as shown in Figure 6, a chopper circuit is utilized to perform simple ON/OFF control of the BR. The TCU of the traction unit is responsible for regulating the BR’s operation. If the voltage of the DC traction network is higher than the pre-set threshold, the BR will be switched in to consume regenerative power from the vehicle, otherwise the BR is switched off.
The most direct way to calculate the electrical power consumed by the BR is to measure its operational current, by multiplying the current and the voltage of DC traction network the power can be calculated. Yet, such method will introduce another unnecessary sensor to the traction unit’s operation, and it suffers from the same false alert issue as the temperature sensor did.
To overcome such a problem, in this study, a novel power calculation solution is proposed to utilize only the voltage of DC traction network for input power calculation. As the voltage of DC traction network is the necessary electrical variable that needs to be continuously measured, the proposal will not introduce any additional senor, which leaves a sensorless manner to the task of temperature monitoring/estimation.
The difficulty of utilizing only voltage for power calculation is due to the fact that the resistance of BR unit will be affected by the temperature rise, which leaves a strong uncertainty to the power calculation problem. In the sections above, the thermal dynamic and the energy model of the BR is derived, which opens the possibility to combine the power calculation and the temperature estimation as a unified calculation to perform sensorless operational temperature estimation of the BR.
As a resistive component, the heat production of BR by absorbing electrical power can be presented by:
Pbr – The electrical power consumed by the resistor;
Udc – The voltage of the DC traction network;
Rbr – The real-time resistance of the BR;
D – The duty cycle of the chopper circuit;
As the real-time resistance of the BR is changing according to the temperature, the calculation of input power shall also consider the temperature impact. Due to the fact that the resistor piece of BR is currently made by alloy material, the resistance of such material has a quasi-linear relationship to its temperature, to simplify the calculation, the relationship of BR’s resistance over temperature are considered by:
R0 – The initial resistance of the BR piece, under 25°C environment;
Tt – The real-time temperature of the BR piece;
T0 – The initial temperature of the BR piece (i.e. 25°C);
α – The temperature-resistance coefficient;
By combining (14), (15) and the temperature calculation process of BR, a novel temperature estimation algorithm can be formulated as the flow chart shown in Figure 7. The proposal combines the proposed voltage-based input power calculation, energy-model based temperature estimation and parameter updating to formulate a close-loop Iterative calculation that provides real-time temperature of the BR.
3. Simulation-base validation and comparison
To validate the effectiveness of the proposed real-time sensorless operational temperature estimation method, simulation-based verification and comparison is carried out with the proposed methodology with more conventional finite element method (FEM) based temperature-field simulation.
3.1 FEM model established using Ansys Fluent for comparison
The FEM-based method is well-known for its accuracy, which makes it a good and qualified target for comparison. To carry out the comparison, a simplified 3D-model of a typical BR bank as shown in Figure 2 is established using Ansys Fluent fluid simulation environment. The model has similar structure as the benchmark study case of BR. The rendered model is as shown in Figure 8. The following FEM-based simulation and the corresponding results are for comparison purpose.
In Figure 9, the simulation results of a steady state temperature field of the established model are presented. As stated in the above section, the proposed real-time sensorless operational temperature estimation method selects the resistor layer in the middle area of the BR bank’s built-in cooling-air duct, the simulation results are selected to be of the layer at the middle of the simulated space for comparison purpose.
In this simulation, the input power from BR is set to be 300kW, the steady-state temperature field and its temperature distribution is given. The highest temperature is 326.05°C appears at the resistor which is near the outlet of the cooling-air duct.
3.2 Temperature rising simulation results of proposed methodology
To carry out comparison, the same input condition of the BR is set for the proposed sensorless temperature estimation method. As the proposal is a real-time method instead of a steady state solver, the whole temperature rising process of the BR is simulated. The simulation results for resistor temperature and the air temperature are given in Figures 10 and 11, respectively.
It can be derived from the simulation results that the highest temperature is 306.52°Cappears at the resistor which is near the outlet of the cooling-air duct. By comparing the FEM-based simulation results and the simulation results using proposed methodology, the relative error between these two simulation results is 5.9% (taking FEM-based simulation results as reference). Such error is obviously acceptable for engineering practice when considering the huge difference in computational burden and the real-time manner of the proposed methodology.
In Table 1, the simulation results of both FEM-based simulation and proposed real-time estimation regarding highest temperature under different input power, which is the most important for alert and protection, are given. The input power of these is set to be from 50 to 500kW, respectively. The relative error for such range of operational temperature is relatively small and all of which are below 10%.
3.3 Transient thermal dynamic response and comparison
In this part, the simulation results of the of the proposed method regarding its transient dynamic response is presented and demonstrated. Two major study case are presented which are the thermal dynamic of the BR during one-shot braking and periodical braking.
3.3.1 Transient temperature dynamic response of one-shot braking
In the first simulation scenario, the one-shot braking process, which presents the scenario vehicle to brake and to stop at the station for a long time. In this simulated study case, the input power is given as shown in Figure 12.
In Figure 13, the simulated dynamic response of the transient temperature of proposed method and FEM-based method are both presented. In this simulation, the FEM-based method is utilizing the “transient” mode of Ansys Fluent simulation software. Due to the heavy computational burden and limitation of memory, the time interval of this FEM-based simulation has to be set as 1s. It can be seen from the simulation results that the proposed methodology gives similar dynamic when compared with FEM-based simulation results, the maximum relative error of the two dynamic response is 6.23% in this simulation (using FEM-based simulation results as reference).
One noteworthy difference is that the results given is higher than those given by the FEM-based method, which is opposite when considering the relative error in steady-state as listed in Table 1. To the author’s knowledge, this is a result due to the fact that the simulation time step of the proposed method is much smaller than the time interval of FEM-based method, which leads to less absence of energy during the calculation. As the estimated may be higher, the results is still acceptable from the viewpoint of engineering practice.
3.3.2 Transient temperature dynamic response of periodic braking
In the second simulation scenario, the periodic braking process, which presents a more typical operational case that the vehicle brake periodically due to the station-to-station operation of metro. In this simulated study case, the input power is given as shown in Figure 14.
Unfortunately, the memory requirement to carry out this simulation scenario using FEM-based method is way too hard to achieve, thus, only the simulation results using proposed method can be given, which are shown in Figure 15.
4. HIL-based combinational test for validation
In order to validate the effectiveness of the proposed sensorless temperature estimation method and its deployability in real-world microprocessor that is used in engineering practical. A HIL-based combinational test of the proposal is carried out with the test setup as shown in Figure 16. In this test, the TMS320F28379D microprocessor is utilized and serve as the main processor of a TCU. A typical FOC-based motor drive controller, the DC voltage regulation of DC traction network by ON/OFF control of BR are both deployed. The SPEEDGOAT HIL real-time target machine is utilized as the HIL platform of the system, in which the DC traction network including substation (24-pulse diode-based rectifier), the line impedance and the vehicle dynamic (i.e. motor dynamic and BR dynamic) are modeled.
The HIL-based test results of a typical braking process is given in Figure 17. It can be seen from the results that the TCU carried out the BR temperature estimation, the duty-cycle regulation of DC network voltage and the braking (which provides the regenerative power) at the same time. The temperature rising of the braking resistor follows the typical thermal dynamic of BR.
5. Conclusion
In this study, an energy model-based sensorless operational temperature estimation methodology is proposed. The main contribution of the proposal is that by combining the energy model and the voltage-based power calculation, the combined iterative calculation algorithm successfully addressed the influence of temperature on the resistance of BR, thus, opening a new way to achieve the real-time estimation of the operational temperature of the BR onboard metro vehicle using only the mandatory electrical sensor instead of dedicated thermal sensors with acceptable accuracy for engineering practice and good dynamic response. The proposed method is validated by comparison with FEM-based simulation and HIL-based test, the results clearly demonstrated that the proposed method have no dependency of additional sensor, and have good dynamic response, as well as considerable deployability in real-world TCU processor.
Figures
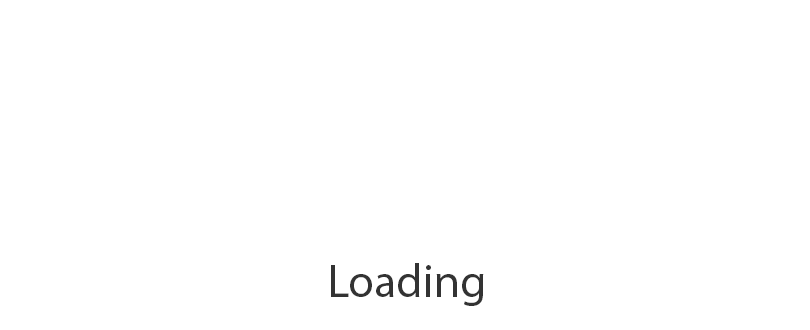
Figure 14
The input power dynamic of the simulation scenario presented in Section 3.3.2
Simulation results and relative error using FEM-based method and proposed method
Input Power/kW | Estimated temperature using proposed method/°C | Simulated results using FEM/°C | Relative error/% |
---|---|---|---|
50 | 70.33 | 71.01 | 0.96 |
100 | 117.49 | 122.02 | 3.71 |
200 | 211.92 | 224.03 | 5.4 |
300 | 306.52 | 326.05 | 5.99 |
400 | 401.21 | 428.06 | 6.27 |
500 | 495.95 | 530.08 | 6.44 |
Source(s): Author’s own work
References
Gao, J., Zheng, X., Li, Y., Xie, B., Gong, S., & Wang, L. (2021). Research on selection and protection strategy of voltage-limiting resistor in traction converters. Electric Drive for Locomotives, 2, 87–91.
Hu, C., Qin, J., Zhu, T., Peng, P., & Wang, Z. (2021). Analysis of urban rail resistance braking system and IGBT loss evaluation. In International Conference on Electrical and Information Technologies for Rail Transportation, Singapore: Springer Singapore (pp. 250–256).
Lee, D. D., Kang, H. I., & Shim, J. M. (2015). Thermal analysis and temperature characteristics of a braking resistor for high-speed trains for changes in the braking current. Journal of the Korean Physical Society, 67, 975–979.
Lee, D. D., Shim, J. M., & Hyun, D. S. (2013). Temperature characteristics analysis of braking resistor for high speed train. Studies in Informatics and Control, 22(1), 26.
Li, K., & Zhang, Z. (2005). Design of ground braking resistor in Guangzhou metro line 4. Electrical Drive for Locomotives, 5, 43–46.
Liu, H. (2018). Research on over-temperature protection of vehicle brake resistance for Xi'an metro line 2. Modern Urban Transit, 10, 31–34.
Liu, Y., Shi, J. C., & Wu, H. D. (2002). Calculation of ventilation and temperature-rise for brake resistance. Technology for Electric Locomotives, 25(2), 11–14.
Neale, A., Derome, D., Blocken, B., & Carmeliet, J. (2007). Determination of surface convective heat transfer coefficients by CFD. In 11th Canadian Conference on Building Science and Technology Banff, Alberta.
Sun, X., Shao, C., Wu, Y., Yang, D., Yang, N., & Li, Y. (2015a). Study on the brake resistor and energy consuming brake process of hybrid electric vehicle. In 2015 International Conference on Electrical Systems for Aircraft, Railway, Ship Propulsion and Road Vehicles (ESARS) (pp. 1–6). IEEE.
Sun, X., Wang, Y.C., Shao, C.M., Wang, G.Z., & Wang, L. (2015b). Experimental research on braking resistor heat dissipation performance of hybrid electric vehicle. Vehicle & Power Technology, 3, 25–29.
Wang, R. (2019). Analysis and treatment of brake resistance over-temperature fault during long-term down-slope braking of metro train. Electric Locomotives & Mass Transit Vehicles, 2, 71-73, 86.
Further reading
Desportes, G., Flerlage, H., Berasategi, A., Gassert, M., & Gassert, M.G. (2016). New dependable rolling stock for a more sustainable, intelligent and comfortable rail transport in Europe- D1.3 – performance compilation of rail traction system/equipment (Ref. Ares(2016) 3381208 - 13/07/2016). Shaft2Rail (EU H2020).
Ding, J., & Tang, Y. (2012). CFD simulation for brake resistor of rail vehicle. Electric Drive for Locomotives, 4, 37–39.
Leoutsakos, G., Deloukas, A., Sarris, K., Apostolopoulos, I., Mamaloukakis, C., Kyriazidis, D., Bensmann, A., & Hanke-Rauschenbach, R. (2023). Metro traction power measurements sizing a hybrid energy storage system utilizing trains regenerative braking. Journal of Energy Storage, 57, 106115.
Zhou, A., Du, C., Peng, Z., Peng, Q., & Qin, D. (2020). Rotor temperature safety prediction method of PMSM for electric vehicle on real-time energy equivalence. Mathematical Problems in Engineering, 2020, 1–10.
Acknowledgements
This work is supported by the Fund of China Academy of Railway Sciences Corporation Limited (2022YJ230) and the Scientific Research Projects of China Association of Metros (CAMET-KY-2022039).