Abstract
Purpose
This paper endeavors to create a predictive model for the energy consumption associated with the multi-material fused deposition modeling (FDM) printing process.
Design/methodology/approach
An online measurement system for monitoring power and temperature has been integrated into the dual-extruder FDM printer. This system enables a comprehensive study of energy consumption during the dual-material FDM printing process, achieved by breaking down the entire dual-material printing procedure into distinct operational modes. Concurrently, the analysis of the G-code related to the dual-material FDM printing process is carried out.
Findings
This work involves an investigation of the execution instructions that delineate the tooling plan for FDM. We measure and simulate the nozzle temperature distributions with varying filament materials. In our work, we capture intricate details of energy consumption accurately, enabling us to predict fluctuations in power demand across different operational phases of multi-material FDM 3D printing processes.
Originality/value
This work establishes a model for quantifying the energy consumption of the dual-material FDM printing process. This model carries significant implications for enhancing the design of 3D printers and advancing their sustainability in mobile manufacturing endeavors.
Keywords
Citation
Yang, W., Liu, Y., Chen, J., Chen, Y. and Shang, E. (2024), "Process-based modeling of energy consumption for multi-material FDM 3D printing", Journal of Intelligent Manufacturing and Special Equipment, Vol. 5 No. 1, pp. 190-202. https://doi.org/10.1108/JIMSE-10-2023-0008
Publisher
:Emerald Publishing Limited
Copyright © 2024, Wenzhen Yang, Yu Liu, Jinghua Chen, Yanqiu Chen and Erwei Shang
License
Published in Journal of Intelligent Manufacturing and Special Equipment. Published by Emerald Publishing Limited. This article is published under the Creative Commons Attribution (CC BY 4.0) licence. Anyone may reproduce, distribute, translate and create derivative works of this article (for both commercial and non-commercial purposes), subject to full attribution to the original publication and authors. The full terms of this licence may be seen at http://creativecommons.org/licences/by/4.0/legalcode
1. Introduction
Fused deposition modeling (FDM) is widely considered one most cost-effective additive manufacturing (AM) techniques for building a 3D complex structure by extruding the liquified thermoplastic or thermoset filaments through a small diameter nozzle (Medellin-Castillo and Zaragoza-Siqueiros, 2019). In this context, the analysis of energy consumption is one prerequisite to evaluate its printing capacity and manufacturing sustainability (May et al., 2013). For a FDM printing process, Peng (2016) proposed a two-level energy analysis method based on the energy flow during the printing process. The primary energy is the thermal energy required for melting the printing filaments, and the secondary energy is the auxiliary energy input to drive the mechanical movements, auxiliary temperature fields, etc. Ajay et al. (2016) obtained the impacts of printing accuracy, printing speed and temperature on the energy consumption and found that the heat energy consumption in the printing process accounts for about 40% of the total power consumption. Therefore, Le Bourhis et al. (2013) and Le Bourhis et al. (2014) analyzed each printing parameter comprehensively and established a prediction model on the power factor of the consumable filament material.
In a study involving three distinct FDM printers, Clemon et al. (2013) observed that a significant portion of the energy was primarily allocated to the heating elements during the printing process. Subsequently, Mognol et al. (2006) initiated an investigation into the influence of various in-process printing parameters on energy consumption. Their findings revealed that not only heating elements but also the spatial arrangement of printed parts could significantly affect the overall power consumption during the printing operation. Balogun et al. (2014) conducted a unified analysis involving three distinct FDM printers and summarized the power consumption characteristics during the primary operational phases of these printers. Their findings indicated that continuous printing under full task requirements reduced the loss of thermal energy (Balogun et al., 2014, 2015). Moreover, a recent investigation by Azadeh et al. (2018) explored the impact of layer thickness and packing density on the mechanical properties of printed parts. Surprisingly, the researchers discovered that achieving higher dimensional accuracy did not necessarily translate to increased power consumption, as observed in traditional subtractive manufacturing processes. For precise energy consumption prediction, Yosofi et al. (2018) recently segmented the FDM printing process into distinct operational stages and developed energy consumption models for each stage through experimental analysis. In a parallel effort, Ajay et al. (2017) examined the printer’s motion execution instructions. They proposed an energy-saving approach by deactivating other axis drive motors during single axial movements, leading to a 25% reduction in energy consumption with this innovative printing strategy.
Existing research in the field has predominantly focused on single-material FDM 3D printing, often making the assumption of a constant temperature field during the printing process. However, the proliferation of FDM printers equipped with multiple extruders has been a transformative development in both academic and industrial domains (Espalin et al., 2014). These multi-extruder printers possess the capability to directly manufacture intricate functional 3D parts (Roach et al., 2019). In multi-material FDM 3D printing, the materials involved may exhibit significantly different melting temperatures, necessitating frequent power adjustments, including switching on and off, as well as increasing and decreasing power levels during the printing process (Yin et al., 2018; Lin et al., 2018). These factors introduce complexity in assessing electrical energy consumption accurately. As a response to these challenges, this paper aims to present a comprehensive model for quantifying the power requirements essential to operate a dual-extruder FDM 3D printer. The insights derived from this model will be instrumental not only in optimizing multi-material FDM design but also in enhancing various forms of AM processes.
2. Experimental section
As shown in Figure 1, our experimental setup for energy analysis employed a dual-extruder FDM 3D printer, namely Ultimaker 3 (from Ultimaker Inc.). For the printing process, two different filament materials, Acrylonitrile Butadiene Styrene (ABS) and polylactic acid (PLA), were employed directly. Their respective material properties are outlined in Table 1. Notably, we designated the “ABS” nozzle and the “PLA” nozzle to correspond with their respective material types. The energy consumption analysis was structured into three defined modules, each aligned with specific aspects of the FDM infrastructure: (1) The motion module pertained to the energy consumed during the motion movements of the three axes and the extruder motor. (2) The heating module encompassed the energy requirements associated with two liquefier heaters and one building platform heater. (3) The peripheral module, which functioned in a constant power consumption mode, included components such as the LCD, cooling fan, main control board and other peripheral devices.
The experimental configuration is illustrated in Figure 2. The FDM 3D printer was connected to a constant voltage power supply, specifically a DC (direct-current) driven model (62015L, Chroma ATE Inc), enabling us to monitor both the driving current and voltage. Figure 2 (a) illustrates our setup, which involved the utilization of an oscilloscope, the DSO-X3024 T (Keysight, Inc.), for measuring the internal MOSFET operating frequency, set at 1 kHz. In line with the Nyquist Theorem, it is crucial for the data acquisition sampling frequency to be at least twice the source signal frequency. Therefore, we established a sampling frequency of 10 kHz, which is approximately ten times the signal frequency, as suggested by Kehtarnavaz and Kim (2005) and Candes and Wakin (2008). To facilitate power evaluation, precision resistors were incorporated in series with the FDM printer’s power supply. We then monitored the voltages across these resistors using the DAQ NI9205 device from National Instruments, Inc., which allowed us to calculate the currents precisely as needed for power assessment. All testing procedures were conducted under room temperature conditions.
In the context of multi-material FDM 3D printing, we conceptualized a printable cylindrical model featuring a “Yin” and “Yang” design, as illustrated in Figure 3. This model, with a height of 2.5 mm and a diameter of 30 mm, draws inspiration from Chinese philosophy, symbolizing two principles: “Yin,” representing negativity, darkness and femininity, and “Yang,” representing positivity, brightness, and masculinity. To execute the printing process, the part was initially sliced into individual printing layers, each having a thickness of 0.2 mm. During the printing of each layer, the ABS filament was first extruded out from the “ABS” nozzle and deposited in the “Yin” section, accompanied by a gradual increase in nozzle temperature from 200 to 240 °C. In contrast, the PLA filaments were extruded out from the “PLA” nozzle into the “Yang” section, maintaining a constant heating temperature of 150 °C. Throughout the printing process, we continuously recorded real-time data, encompassing the driving current and voltage, directly to the laptop for further analysis.
3. Results and discussion
The assessment of power consumption for the FDM printer commenced with the calibration of its idle mode. This involved measuring the minimal power required to operate the peripheral components, including the control motherboard, the LCD and the cooling fan. Notably, the power consumption during the idle mode remained constant throughout the study. Subsequently, the FDM entered the preheating mode, during which the print bed was heated to its predetermined temperature. Following this, the printing nozzle began heating to facilitate filament melting. For the FDM 3D printer, the “ABS” nozzle was directly heated to a temperature of 240 °C, slightly surpassing the melting point of ABS material. This specific nozzle temperature was consistently maintained during the printing of ABS material. In cases where both ABS and PLA materials were being printed, the “ABS” and “PLA” nozzles were individually heated to their respective standby temperatures, specifically 200 °C for ABS and 150 °C for PLA.
As illustrated in Figure 4, when transitioning from printing with PLA to ABS material, the printer exhibited a notable behavior. Instead of completely deactivating its input power, it appeared to adapt by maintaining the nozzle temperature just below the melting point of PLA. This adjustment persisted until the subsequent printing cycle began. Simultaneously, the printer initiated an increase in electrical power to facilitate the melting of ABS, following its designated heating profile. These profiles were established based on the heating characteristics of both ABS and PLA materials. Notably, during the printing process, the temperatures of the two printing nozzles underwent frequent adjustments, leading to fluctuations in power consumption, as depicted in Figure 5.
Upon completion of the 3D printing process, the FDM printer transitioned into an end mode. During this phase, the printer kept both nozzles at an elevated temperature for a certain duration, serving the purpose of preventing any potential nozzle clogging caused by excess printing material. Hence, in accordance with Yosofi et al. (2018), the total power consumption
After gathering the data from Table 2 and other possible printing parameters, Figure 6a illustrates the power curve for heating the build plate from room temperature to 80 °C by executing the corresponding G-code. The graph reveals that the maximum power required for heating the build plate reached 144 w, thus contributing to the higher mean power during the preheating stage. Notably, the build plate’s power consumption accounted for more than 50% of the total power utilized throughout the entire printing process. Subsequently, Figure 6b presents the heating power consumption of the nozzle as it underwent a temperature increase from room temperature to 220 °C. The FDM 3D printer employed a straightforward control strategy, as depicted in Figure 6c. In this strategy, when the temperature needed to rise, it was heated at full power, and when the temperature needed to decrease, the heating power was completely deactivated until the preset temperature was reached. At that point, it shifted to a low-power mode to maintain a constant temperature. Finally, Figure 6d showcases the power consumption of the motion motor module, which is responsible for the printer’s movement during the printing process.
In summary, Figure 7 illustrates the power consumption curve for a complete cycle of 3D printing. Within this figure, we can discern and accurately calculate the power curves for all operational modes during 3D printing by directly extracting the pertinent commands from the G-code file, as detailed in Table 3.
With an initial velocity of
Given that the overall movement distance of the printer is constrained, and considering that the movement of G1 command follows variable acceleration. The time required for the printer to execute this instruction
Based on Equations (6) and (7), we can get the estimation of the temperature and the time for the printing process operation modes in FDM, as shown in Figure 8. Furthermore, we can create power and time diagrams based on the measured temperature and power curves. The comprehensive analysis of power consumption in FDM follows the outlined flowchart presented in Figure 9.
The overall trend depicted in Figure 10 is established through a theoretical estimation that aligns with the experimental measurements. It’s worth noting that there was a slight discrepancy in time synchronization for the estimation, which could be attributed to two factors. First, variations in the operating environment, including room temperature and the presence of cooling fans, can influence air convection and, consequently, heating efficiency. Second, differences in the heating efficiencies of the two nozzles might contribute to the observed variations. In Figure 10, while there is a certain deviation between the predicted and actual values, the predicted power map effectively captures the amplitude of fluctuation and the temporal range of power changes during the dual-material printing process.
4. Conclusion
In this study, we have integrated an analysis of unit energy consumption with a thorough examination of FDM printer instructions. By employing system parameter calibration and in-depth G-code analysis, we’ve introduced a method for predicting fluctuations in power demand during multi-material FDM printing. This method holds significant potential for enhancing the reliability of FDM printer operation, especially in energy-constrained environments. It is important to note that the accuracy of this method depends on the prediction of temperature, which, in turn, makes it sensitive to environmental conditions and variations.
Figures
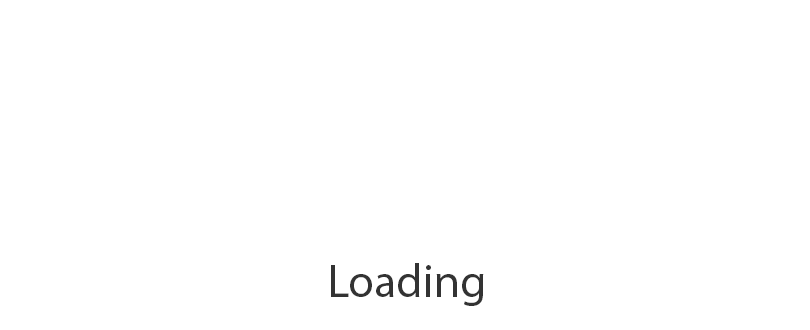
Figure 6
The power requirements for the printer nozzle and build plate under specified temperature conditions, (a) the power required to heat the build plate to 80 °C; (b) the power required to heat the nozzle to 220 °C; (c) the power required for of nozzle heating, which includes heating to 250 °C, cooling down to 100 °C, and then reheating to 195 °C; (d) the power requirements of nozzle movement at 35 mm/s with heating
Properties of 3D printing materials
Materials | ABS | PLA |
---|---|---|
Nozzle temperature/°C | 230 | 200 |
Build plate temperature/°C | 80 | 60 |
Standby temperature/°C | 200 | 150 |
Fan speed/% | 5 | 100 |
Print speed/ | 40 | 40 |
Source(s): Authors own work
The power consumption of the tested instruction
Parameter or state | G-code instruct | Power (W) |
---|---|---|
Idle | \ | 9 |
Build plate warm up | \ | 144 |
Build plate maintain 80 °C | \ | 72 |
Single nozzle warms up | M109 S M104 S | 28 |
Heat the nozzle until the temperature reaches 220 °C | M109 S220 | 28 |
XYZ axis motion and feeder motion | G1F1200 X()Y()Z()E() | 30 |
Source(s): Authors own work
The detailed information by parsing G-codes
G-code | Behavior description |
---|---|
M109 S205 | Heat the nozzle until the temperature reaches |
G0 F15000 X9 Y6 Z2 | The nozzle moves to X9, Y6, Z2 coordinate points at a speed of 15,000 |
G280 | Nozzle returns to the origin |
G1 F1500 E−6.5 | The extruder draws back |
M204 S625 | Maximum accelerator |
M205 X6 Y6 | XY axis maximum jerk |
G0 F4285.7 X67.619 Y104.127 Z0.27 | The nozzle moves to |
M204 S500 | Maximum accelerator |
M205 X5 Y5 | XY axis maximum jerk |
G1 F1500 E0 | Extrude material to |
G1 F1200 X96.89 Y94.159 E0.02172 | Nozzle moves to |
Source(s): Authors own work
References
Ajay, J., Rathore, A.S., Song, C., Zhou, C. and Xu, W. (2016), “Don't forget your electricity bills! An empirical study of characterizing energy consumption of 3D printers”, Proceedings of the 7th ACM SIGOPS Asia-Pacific Workshop on Systems, pp. 1-8, doi: 10.1145/2967360.2967377.
Ajay, J., Song, C., Rathore, A.S., Zhou, C. and Xu, W. (2017), “3DGates: an instruction-level energy analysis and optimization of 3D printers”, ACM SIGPLAN Notices, Vol. 52 No. 4, pp. 419-433, doi: 10.1145/3093336.3037752.
Azadeh, H., Lin, L., Haghighi, A. and Li, L. (2018), “Study of the relationship between dimensional performance and manufacturing cost in fused deposition modeling”, Rapid Prototyping Journal, Vol. 24 No. 2, pp. 395-408, doi: 10.1108/RPJ-11-2016-0177.
Balogun, V.A., Kirkwood, N.D. and Mativenga, P.T. (2014), “Direct electrical energy demand in fused deposition modelling”, Procedia CIRP, Vol. 15, pp. 38-43, doi: 10.1016/j.procir.2014.06.029.
Balogun, V.A., Kirkwood, N. and Mativenga, P.T. (2015), “Energy consumption and carbon footprint analysis of fused deposition modelling: a case study of RP stratasys dimension SST FDM”, International Journal of Scientific and Engineering Research, Vol. 6 No. 8, pp. 1-6.
Candes, E.J. and Wakin, M.B. (2008), “An introduction to compressive sampling”, IEEE Signal Processing Magazine, Vol. 25 No. 2, pp. 21-30, doi: 10.1109/msp.2007.914731.
Clemon, L., Sudradjat, A., Jaquez, M., Krishna, A., Rammah, M. and Dornfeld, D. (2013), “Precision and energy usage for additive manufacturing”, ASME International Mechanical Engineering Congress and Exposition, Vol. 56185, V02AT02A015, doi: 10.1115/IMECE2013-65688.
Espalin, D., Ramirez, J.A., Medina, F. and Wicker, R. (2014), “Multi-material, multi-technology FDM: exploring build process variations”, Rapid Prototyping Journal, Vol. 20 No. 3, pp. 236-244, doi: 10.1108/RPJ-12-2012-0112.
Kehtarnavaz, N. and Kim, N. (2005), Digital Signal Processing System-Level Design Using LabVIEW, Elsevier, Oxford.
Le Bourhis, F., Kerbrat, O., Dembinski, L., Hascoet, J.Y. and Mognol, P. (2014), “Predictive model for environmental assessment in additive manufacturing process”, Procedia CIRP, Vol. 15, pp. 26-31, doi: 10.1016/j.procir.2014.06.031.
Le Bourhis, F., Kerbrat, O., Hascoet, J.Y. and Mognol, P. (2013), “Sustainable manufacturing: evaluation and modeling of environmental impacts in additive manufacturing”, The International Journal of Advanced Manufacturing Technology, Vol. 69 No. 9, pp. 1927-1939, doi: 10.1007/s00170-013-5151-2.
Lin, W., Shen, H., Xu, G., Zhang, L., Fu, J. and Deng, X. (2018), “Single-layer temperature-adjusting transition method to improve the bond strength of 3D-printed PCL/PLA parts”, Composites Part A: Applied Science and Manufacturing, Vol. 115, pp. 22-30, doi: 10.1016/j.compositesa.2018.09.008.
May, G., Taisch, M., Prabhu, V.V. and Barletta, I. (2013), “Energy related key performance indicators-state of the art, gaps and industrial needs”, IFIP International Conference on Advances in Production Management Systems, Vol. 414, pp. 257-267, doi: 10.1007/978-3-642-41266-0_32.
Medellin-Castillo, H.I. and Zaragoza-Siqueiros, J. (2019), “Design and manufacturing strategies for fused deposition modelling in additive manufacturing: a review”, Chinese Journal of Mechanical Engineering, Vol. 32 No. 1, pp. 1-16, doi: 10.1186/s10033-019-0368-0.
Mognol, P., Lepicart, D. and Perry, N. (2006), “Rapid prototyping: energy and environment in the spotlight”, Rapid Prototyping Journal, Vol. 12 No. 1, pp. 26-34, doi: 10.1108/13552540610637246.
Peng, T. (2016), “Analysis of energy utilization in 3D printing processes”, Procedia CIRP, Vol. 40, pp. 62-67, doi: 10.1016/j.procir.2016.01.055.
Roach, D.J., Hamel, C.M., Dunn, C.K., Johnson, M.V., Kuang, X. and Qi, H.J. (2019), “The m4 3D printer: a multi-material multi-method additive manufacturing platform for future 3D printed structures”, Additive Manufacturing, Vol. 29, 100819, doi: 10.1016/j.addma.2019.100819.
Yin, J., Lu, C., Fu, J., Huang, Y. and Zheng, Y. (2018), “Interfacial bonding during multi-material fused deposition modeling (FDM) process due to inter-molecular diffusion”, Materials and Design, Vol. 150, pp. 104-112, doi: 10.1016/j.matdes.2018.04.029.
Yosofi, M., Kerbrat, O. and Mognol, P. (2018), “Energy and material flow modelling of additive manufacturing processes”, Virtual and Physical Prototyping, Vol. 13 No. 2, pp. 83-96, doi: 10.1080/17452759.2017.1418900.
Acknowledgements
This work was supported by the National Natural Science Foundation of China (Grant No. 51875253), the Fundamental Research Funds for the Central Universities (Grant No. JUSRP21910) and Postgraduate Research and Practice Innovation Program of Jiangsu Province [Grant numbers KYCX21-2032].
Corresponding author
About the authors
Wenzhen Yang received the B.S. degree from the College of Computer and Information Science, Southwest University, Chongqing, China, in 2012. He is currently pursuing the Ph.D. degree with the School of Mechanical Engineering, Jiangnan University. His research interests include 3-D printing, soft electronics, and wearable sensors.
Yu Liu received the B.S degree in control science and engineering from the Harbin Institute of Technology, Harbin, China, the M.S. degree in mechanical engineering from Kyungpook National University, Daegu, South Korea, and the Ph.D. degree from the University of Western Ontario, London, ON, Canada. He is currently a Professor and a Vice-President with the School of Mechanical Engineering, Jiangnan University, Wuxi, China. He has authored over 80 peer-reviewed literature publications and three book chapters, and holds more than 60 patents, including 40 registered U.S. patents. His current research interests include additive manufacturing, 3-D printed electronics, precision mechatronics, and micro/nano manufacturing. He is leading the Institute of Precision Intelligent System Engineering (iPISE) for establishing optimal solutions to the emerging 3-D mechatronics.
Jinghua Chen received a B.S. degree from the College of Mechanical Engineering, Jiangnan University, Wuxi, China, in 2017. His research interests include energy management and green manufacturing.
Yanqiu Chen received a B.S degree in computer science and technology, the Ph.D. degree in vehicle application engineering from Southwest Jiaotong University, Chengdu, China. He is currently an associate professor and graduate supervisor with the School of Mechanical Engineering, Jiangnan University, Wuxi, China. He has led over 20 research projects, including national major special sub-projects, Jiangsu provincial postdoctoral fund, and enterprise-related projects. He has also participated as a key researcher in 3 national natural science foundation projects and 2 Jiangsu provincial key research and development projects. He successfully achieved direct-writing 3D printing of silicon foam materials through additive manufacturing, solving critical issues in automatic control. He has published over 30 academic papers and holds more than 10 invention patents. His current research areas include additive manufacturing, intelligent factories, robot control, and energy management. He specializes in software design and development, control algorithms, and related fields.
Erwei Shang received a B.S. degree from the College of Mechanical Engineering, Zhengzhou University, Henan, China, in 2017. He is currently pursuing the Ph.D. degree with the School of Mechanical Engineering, Jiangnan University. His research interests include 3-D printing, soft sensors, and topological optimization.