Abstract
Purpose
Managing supply chains (SCs) for sustainability often results in conflicting demands, which can be conceptualized as sustainability tensions. This paper studies sustainability tensions in electronics SC contexts and the related management responses by applying a paradox perspective.
Design/methodology/approach
A single case study on the electronics SC is conducted with companies and third-party organizations as embedded units of analysis, using semi-structured interviews that are triangulated with publicly available data.
Findings
The study identifies tension elements (learning, belonging, organizing and economic performing) conflicting with general social–ecological objectives in the electronics SC. The results indicate a hierarchal structure among the sustainability tensions in SC contexts. The management responses of contextualization and resolution are assigned to the identified tensions.
Practical implications
Framing social–ecological objectives with their conflicting elements as paradoxical tensions enables organizations and SCs to develop better strategies for responding to complex sustainability issues in SC contexts.
Originality/value
The study contributes toward filling the gap on paradoxical sustainability tensions in SCs. Empirical insights are gained from different actors in the electronics SC. The level of emergence and interconnectedness of sustainability tensions in a larger SC context is explored through an outside-in perspective.
Keywords
Citation
Zehendner, A.G., Sauer, P.C., Schöpflin, P., Kähkönen, A.-K. and Seuring, S. (2021), "Paradoxical tensions in sustainable supply chain management: insights from the electronics multi-tier supply chain context", International Journal of Operations & Production Management, Vol. 41 No. 6, pp. 882-907. https://doi.org/10.1108/IJOPM-10-2020-0709
Publisher
:Emerald Publishing Limited
Copyright © 2021, Axel Georg Zehendner, Philipp C. Sauer, Patrick Schöpflin, Anni-Kaisa Kähkönen and Stefan Seuring
License
Published by Emerald Publishing Limited. This article is published under the Creative Commons Attribution (CC BY 4.0) licence. Anyone may reproduce, distribute, translate and create derivative works of this article (for both commercial and non-commercial purposes), subject to full attribution to the original publication and authors. The full terms of this licence may be seen at http://creativecommons.org/licences/by/4.0/legalcode
1. Introduction
Managing sustainability in supply chains (SCs) is often associated with the emergence of numerous tensions and conflicts (Brix-Asala et al., 2018; Xiao et al., 2019). In sustainable supply chain management (SSCM), tensions typically arise from divergent elements that conflict with the realization of social–ecological objectives in SCs (Govindan et al., 2021). Probably, the most common sustainability tension for organizations is the conflict between short-term economic profitability and long-term integration of social–ecological sustainability (Glover, 2020; Slawinski and Bansal, 2015; Wu and Pagell, 2011). Nevertheless, sustainability tensions also emerge from divergent activities and underlying elements in the wider context (or system) (e.g. Brix-Asala et al., 2021; Sandberg, 2017; Xiao et al., 2019). Limited visibility and knowledge in SCs (Carter et al., 2015), conflicting institutional environments (Brix-Asala et al., 2021; Sauer and Seuring, 2018), and lacking contractual relationships and power (Grimm et al., 2014; Touboulic et al., 2014) are examples of the many elements diverging from the implementation of social–ecological sustainability in SCs.
To successfully respond to sustainability tensions, the paradox perspective has emerged in corporate sustainability (Van der Byl and Slawinski, 2015; Hahn et al., 2015) and SSCM research (Brix-Asala et al., 2018; Matthews et al., 2016; Xiao et al., 2019). Instead of avoiding contradictions that pose the risk of a later escalation, paradox thinking advocates acknowledging and embracing tensions to develop better responses and management strategies (Van der Byl and Slawinski, 2015; Smith and Lewis, 2011). However, most business studies have viewed and addressed tensions by adopting the instrumental “win-win” and “trade-off” perspectives, which typically prioritize economic outcomes over social–ecological concerns (Xiao et al., 2019; Zhang et al., 2021). In addition to leaving the underlying tensions and paradoxes unresolved, the instrumental perspectives are also criticized for being too simplistic for the multi-faceted nature of sustainability and its management (Van der Byl and Slawinski, 2015; Hahn et al., 2015). Focusing solely on activities benefitting the financial performance restricts the potential contribution to sustainable development and today's grand challenges (Hahn et al., 2018; Manzhynski and Figge, 2020). Yet, few studies have adopted an explicit paradox perspective to explore sustainability tensions in SC contexts (Zhang et al., 2021). Moreover, empirical insights into how to address sustainability tensions in general (e.g. Van der Byl and Slawinski, 2015) and particularly in SCs (e.g. Brix-Asala et al., 2018; Matthews et al., 2016; Xiao et al., 2019) are scarce. To contribute to closing these gaps, our study focuses on the global electronics SC and seeks to answer the following questions:
What types of sustainability tensions can be identified within SC contexts?
How do companies respond to these sustainability tensions?
By conducting a single case study on the electronics SC with multiple embedded units of analysis, our study makes the following contributions to the literature. First, it contributes to research on sustainability tensions through the application of a paradox perspective. By outlining sustainability paradoxes in the electronics SC, it is among the few studies offering empirical insights into sustainability-related paradoxical tensions (e.g. Van der Byl and Slawinski, 2015; Xiao et al., 2019). Second, in addition to identifying different sources of tensions, this study also applies an outside-in perspective to explore the location and interconnectedness of these tensions (and paradoxes) in a larger SC context. The results indicate a hierarchical structure in which tensions from a higher level reinforce those at lower levels. Third, our research identifies specific practices that can be used as response strategies for sustainability tensions. Fourth, this study contributes to the research on multi-tier SCs by outlining the complexities and conflicting elements opposed to the realization of social–ecological objectives in (multi-tier) SCs in the form of paradoxical tensions. The results show that the identified sustainability tension can differ along the multiple tiers of SCs.
The remainder of this paper is structured as follows: First, we introduce the theoretical background and the two frameworks applied in this study. Thereafter, the methodological approach and data analysis are outlined, and the results of the case study are presented. Next, the theoretical and practical implications are discussed, and finally, the paper concludes by acknowledging limitations and outlining future research avenues.
2. Literature review
2.1 Paradox perspective on sustainability tensions
Paradoxical tensions are often defined as “contradictory yet interrelated elements that exist simultaneously and persist over time” (Smith and Lewis, 2011, p. 382). Although paradoxical tensions are inherent across various contexts, the paradoxical nature of divergent elements and tensions only surfaces through their recognition and social construction (Schad et al., 2016; Smith and Lewis, 2011). For these reasons, paradox thinking has been proposed as an approach to cope with contradictory elements by recognizing and explicitly acknowledging the paradoxical tension between these elements (Van der Byl and Slawinski, 2015; Smith and Lewis, 2011). Regarding corporate sustainability, many paradox scholars have suggested that organizations should embrace sustainability tensions instead of avoiding contradictory and interrelated demands (Van der Byl and Slawinski, 2015; Hahn et al., 2015). This means that managers should acknowledge the interconnectedness and interdependence of economic, environmental and social concerns, in order to develop better management strategies and responses (Hahn et al., 2015, 2018). By identifying and embracing sustainability tensions and their divergent elements, paradox thinking creates leeway to contribute to sustainable development by balancing financial outcomes with moral obligations for social and environmental responsibility (Van der Byl and Slawinski, 2015; Hahn et al., 2016, 2018).
Although tensions and paradoxes are frequently recognized in SC contexts (e.g. Schmidt et al., 2017; Wu and Pagell, 2011), only a few studies have adopted an explicit paradox perspective (Zhang et al., 2021) despite its potential for SSCM research (Matthews et al., 2016). Among these, Xiao et al. (2019) identified responses to paradoxical tensions originating from conflicts between cost competitiveness and sustainability. Brix-Asala et al. (2018) investigated SSCM practices addressing paradoxical sustainability tensions in SCs. Wilhelm and Sydow (2018) studied buying firms' management approaches to the coopetition paradox in their supplier network. Sandberg (2017) outlined paradox elements emerging within global sourcing contexts, whereas Zhang et al. (2021) identified multiple paradox elements through a systematic literature review. Carter et al. (2020) used paradox theory to conceptualize the emergence of unintended consequences of SSCM initiatives. Brix-Asala et al. (2021) studied the potential of supplier development for responding to the “base of the pyramid inclusion paradox”.
Even though there is an emerging stream of paradox research related to SCs (Zhang et al., 2021), most empirical research focusing on sustainability paradoxes has remained within intra-organizational contexts (e.g. Xiao et al., 2019) or focused on a single organization (e.g. Brix-Asala et al., 2018). Moreover, empirical insights into paradoxical tensions from the perspectives of different actors in sustainable (multi-tier) SCs and possible responses to these tensions are still missing.
For developing management strategies that can effectively address tensions and paradoxes, understanding their characteristics is fundamental (e.g. Hahn et al., 2015; Lewis, 2000). The theoretical frameworks developed by Smith and Lewis (2011) for the sources of tension in organizational contexts and Hahn et al. (2015) for sustainability tensions in multi-level contexts have significantly contributed to the understanding of tensions and the embeddedness of their divergent elements. Although both frameworks facilitate the characterization of tensions and paradoxes, a combination of these frameworks can create a sounder and more detailed basis for understanding the underlying origins of tensions. Figure 1 presents our amended framework for categorizing sustainability tensions in SC contexts, which replaces the dimensions of the triple bottom line (economic, environmental and social) found in the original framework proposed by Hahn et al. (2015) with the four tension sources introduced by Smith and Lewis (2011). Moreover, the “SC” level is added as another source for tensions and paradoxes in the larger context (or system) (see also Brix-Asala et al., 2021). In this study, we apply this framework for identifying and characterizing sustainability tensions.
As the framework outlines, there are four major sources of tensions: performing, learning, belonging and organizing. Tensions can emerge within and between these four categories, which were initially proposed for characterizing tensions and paradoxes in organizational contexts (Smith and Lewis, 2011). However, these tension elements also emerge within larger contexts and across different levels (e.g. “SC” and “systemic”) (Brix-Asala et al., 2018, 2021; Sandberg, 2017; Smith and Tracey, 2016). This is particularly relevant for identifying and characterizing sustainability tensions that commonly arise within larger contexts, often due to the mismatch of the temporal and spatial scales across different levels (Van der Byl and Slawinski, 2015; Hahn et al., 2015). For instance, sustainability tensions emerge when the short-term sustainability efforts of organizations fail to match the subordinate and long-term sustainability concerns of society and stakeholders (Hahn et al., 2015; Slawinski and Bansal, 2015). Although corporate responses to climate change are required from society's perspective, individual organizations might continue using carbon-intensive business models and production processes to maximize their short-term profits (Slawinski and Bansal, 2015). Table 1 outlines the four main categories of tensions and relates them to a sustainable SC context.
2.2 Management strategies for sustainability tensions
In the literature, different strategies have been identified for responding to tensions (e.g. Schad et al., 2016). Given the complex nature of tensions and particularly paradoxes, responding to them requires virtuous cycles of thinking and acting (Smith and Lewis, 2011). The cycle starts with the recognition and acceptance of a tension and possibly ends in its resolution (Hahn et al., 2015). However, recent studies have found contextualization to be another strategy for responding to sustainability tensions (Brix-Asala et al., 2018; Xiao et al., 2019). Figure 2 depicts the virtuous cycle for responding to sustainability tensions by integrating the contextualization strategy into the original framework proposed by Hahn et al. (2015) and labeling the transitions (depicted as large arrows in Figure 2) between the main response strategies as “A,” “B,” “C,” and “D.”
The response cycle usually starts with the application of an acceptance strategy. Both competing elements (or poles) of tensions are viewed as simultaneously possible despite being inherently in conflict (Smith et al., 2012). Whether consciously or not, organizations and managers seek means for accepting the tensions and learning to live with them (Poole and van de Ven, 1989). When tensions are still latent, organizations might suppress (or avoid) them until the paradoxical nature of divergent elements starts to become more salient and persistent (Smith and Lewis, 2011; Xiao et al., 2019). The acceptance strategy helps in the short term by acknowledging and confronting both elements' incompatibility, instead of trying to resolve the inherent contradiction and getting stuck in debates, which possibly results in unsatisfactory compromises (Lewis, 2000). However, the appropriateness of the acceptance strategy can (and even should) be questioned, particularly considering the world's grand challenges. For example, novel strategies are required to tackle large and unresolved problems, such as climate change and poverty alleviation (Ferraro et al., 2015). Instead of simply accepting the incompatibility of opposing elements, companies can attempt to cognitively transform the understanding of tensions to find ways in which both contradictory elements can be realized (transition A).
Through the application of contextualizing strategies, tensions and paradoxes can be alleviated by putting their interconnected and divergent elements into context (Xiao et al., 2019). The social construction of paradoxes allows organizations to transform the understanding of tensions by showing flexibility in terms of the desired outcomes and expectations – often for achieving subordinate goals and outcomes. Structural challenges and socio-economic differences can be considered when defining social–ecological objectives for making the tensions and paradoxes more workable in global SC contexts (Xiao et al., 2019). Moreover, companies can alleviate tensions through the external contextualization of divergent (or conflicting) elements to customers and other stakeholders (Brix-Asala et al., 2018). Once the understanding of tensions and paradoxes has been cognitively transformed and alleviated through contextualization strategies, organizations can deliberately choose to enter a conversion cycle (transition B) or reinforcing cycle (transition C).
Once the tensions and paradoxes have been made more workable by taking the larger context into account, resolution strategies (separation and synthesis) can be applied. The resolution of tensions involves seeking responses and strategies “of meeting competing demands or considering divergent ideas simultaneously” (Smith and Lewis, 2011, p. 386). Instead of eliminating tensions and paradoxes, resolution involves the transformation of tensions into a more manageable situation without having to resolve the actual tension (Poole and van de Ven, 1989; Smith and Lewis, 2011). Separation strategies facilitate the management of tensions by keeping the opposing poles separated – either through temporal or spatial separation (Hahn et al., 2015; Smith and Lewis, 2011). Temporal separation deals with two contradictory and inter-related poles at different points in time, whereas spatial separation situates them at different social or physical locations (horizontal separation) or at different contextual levels (vertical separation), e.g. “organizational” or “systemic”. Synthesis strategies manage tensions by linking their two contradictory demands. Although the underlying tension remains, the newly introduced elements through synthesis strategies enable the accommodation of the opposing poles (Hahn et al., 2015; Smith and Lewis, 2011).
If the resolution strategies do not yield desirable situations, the actors can reapply the contextualization strategy (transition D). The overall context is reconsidered to further alleviate the tensions and paradoxes. Depending on the perception of the tension and current situation, companies can either apply the acceptance strategy to live with the current form of the tension (transition C) or continue their quest for resolution strategies that will further transform the tension (transition B).
While the abovementioned response strategies can be theoretically applied to all context levels displayed in Figure 1, this study explicitly focuses on SSCM and thus investigates these responses at the “organizational” and “SC” levels.
3. Research methodology
3.1 Research design
An exploratory case study was conducted to identify and understand sustainability tensions in (multi-tier) SC contexts and to identify strategies for responding to them through the application of a paradox perspective. This qualitative approach was selected because it is useful for studying complex phenomena and their real-world context (Voss et al., 2002), such as sustainability tensions in the global electronics SC. Case studies allow the use of multiple data sources that can be triangulated to develop a broader and more nuanced explanation of phenomena.
We used a single-case study approach with multiple embedded units of analysis (Yin, 2014), which are companies and third-party organizations involved in the electronics SC. Besides being known for facing various sustainability issues (e.g. Brix-Asala et al., 2018; Xiao et al., 2019), the electronics SC was also selected for its complex and global structure, which complicates the integration and realization of social–ecological concerns. The electronics SC context represents an extreme case, highlighting a high level of complexity that needs to be overcome when responding to sustainability tensions and paradoxes.
In addition, the focus on the electronics SC enables us to study the subparts of other industries, such as electronic vehicles as part of the automotive industry. We investigated the sourcing and production of vehicle batteries as the main sustainability hotspots, which are considered as side-issues in automotive SCs. This stable context is particularly beneficial for understanding the emergence and connectedness of sustainably tensions (and paradoxes) in SC contexts despite the limited generalizability of empirical evidence in single-case research.
3.2 Data collection
Our sampling strategy sought to mirror a multi-tier SC stetting (e.g. Hofmann et al., 2018) by including companies at different positions in the electronics SC. These companies were selected because of their sustainability management, typically spanning across organizational borders, and their sustainability-centered business model or the strong external pressures to manage sustainability issues. These companies can be categorized as top-tier, mid-tier and lower-tier firms (Table 2). This sampling logic enables a holistic understanding regarding the tensions emerging along the electronics SC and how companies at different positions respond to them. Moreover, we included four third-party organizations (Table 2) to gain additional insights and different perspectives on sustainability topics and related practices. These third parties were selected as they campaign for more social–ecological sustainability in the electronics industry (TP2, TP4) and/or support case companies in addressing specific social–ecological topics (e.g. ethical sourcing of minerals) (TP1, TP2, TP3).
Interviews are an effective way to gain rich, empirical data about a phenomenon of interest (Eisenhardt and Graebner, 2007). The interviewees in this study were selected because of their management involvement and knowledge about the electronics SC. Having several highly knowledgeable interviewees allows capturing diverse perspectives and mitigating potential biases (Eisenhardt and Graebner, 2007). Twenty-five semi-structured interviews were conducted between April 2018 and November 2019, each of which lasting between 22 and 95 min (average: 44 min). Except for one interview, at least two researchers were involved in conducting all interviews. The interview guide centered on the following topics: (1) sustainability-related values and goals of the organizations and other SC members (including suppliers and customers), (2) main challenges and complexities of managing sustainability in multi-tier SCs, and (3) measures taken to implement and ensure sustainability in SCs. All interviews were audio-recorded and transcribed, together with the interviewer notes. To ensure the internal validity of the content, the interviewees were given the possibility to comment on the transcripts and allowed to add further information. Moreover, secondary material (e.g. annual reports, website content) was collected to triangulate the primary data and obtain additional information.
3.3 Data analysis
The data analysis followed the Gioia methodology (Gioia et al., 2013), which has already been applied in previous paradox research (e.g. Xiao et al., 2019). While the data analysis was conducted by two researchers, the results were iteratively discussed with the other authors. As SSCM aims to integrate social–ecological goals into SCs, our analysis focused on “divergent elements” causing tensions and conflicts together with the “social–ecological elements” of the performing dimension (Smith and Lewis, 2011). A detailed coding tree can be provided upon request by the corresponding author. The general coding process is presented as follows.
In the first round, an inductive analysis of the data yielded seven “social–ecological elements” for the electronics SC (Table 3). These elements were structured in the generic multi-tier stages of “extraction and refinement”, “manufacturing”, and “retail and use”. While the social–ecological elements always belong to the (social–ecological) performing category, the second elements of tensions are categorized as belonging (divergent identities and views), learning (need to build upon existing routines and systems), organizing (competing structures and processes) and economic performing (economic goals) (Smith and Lewis, 2011) (Table 3).
In the second round, first-order concepts for “divergent elements” conflicting with the identified social–ecological elements were inductively crafted. The first-order concepts were then condensed into second-order themes related to the literature on sustainability tensions and paradoxes outlined in the theory section. Besides categorizing the divergent elements as belonging, learning, organizing and economic performing, we also adopted an outside-in perspective to determine the emergence level of divergent elements in the larger SC contexts (e.g. “SC”, “systemic”) and their connectedness (Figure 1).
In the third round, “management responses” to sustainability tensions were detected and subsequently categorized as “resolution” (synthesis and separation) and “contextualization” strategies (Figure 2). In our analysis, we sought to identify the rather proactive strategies and practices for responding to tensions and paradoxes and thus neglected the “acceptance” strategy, which either suppresses tensions or keeps them open.
3.4 Validity and reliability
To validate the quality and reliability of qualitative research designs, Yin (2014) proposed four tests. External validity aims for generalizability, which is often challenging in qualitative studies. One key measure here is having a clear sampling logic covering multiple stages and actors in SC studies. Construct validity and reliability must be primarily ensured during data collection. This was implemented by building questions on the research frameworks and linking them to theory. Data triangulation was achieved using (1) multiple sources of data by integrating interviewees along the SC and (2) secondary data sources. Internal validity was considered during the data analysis by matching patterns among the interviews and linking them to the theoretical framework. Reliability aims at ensuring transparency of the research process. As mentioned, interviews were conducted based on a sampling logic and application of an interview guide. Moreover, the interviews were transcribed and analyzed using a qualitative data analysis software (MAXQDA). Overall, much attention was paid to documenting the research process in a transparent and reproducible manner, meeting the demands for sound qualitative empirical research.
4. Findings
This section presents the identified sustainability tensions and the management strategies used for responding to them. Table 3 provides a detailed overview of all our case study findings.
4.1 Sustainability tensions and their divergent elements
As the social–ecological elements of performing constantly represent one element of the sustainability tensions in our analysis, the identified tensions are presented according to the divergent elements of learning, belonging, organizing and economic performing. Table 3 presents the relationships between the seven identified social–ecological elements (column headings) and their conflicting elements (row headings) labeled according to the divergent elements – belonging, learning, organizing and economic performing. In addition, the table displays the occurrence of sustainability tensions among the group of actors in this case study.
4.1.1 Learning elements
Learning elements represent the demand to build upon existing routines and systems for realizing social–ecological goals in SC contexts, which often require radically different or new ways of doing business.
In our sample, many companies struggled with the implementation and realization of their social–ecological goals against the systemic problems in producing countries (Learn1). For example, unenforced laws and difficulties in establishing collaborations with NGOs in Southeast Asia diverge from the social–ecological objectives of ensuring responsible manufacturing and improving the social–ecological performance of SCs (TT3, MT3, MT4). The results also revealed systemic problems in sourcing minerals from Africa and South America, including legal issues (e.g. changing mining regulations), environmental problems (e.g. environmental deterioration and destruction), social issues (e.g. illegal and unregulated mining), and other problems (e.g. absence of relevant infrastructure) (e.g. LT1, LT2, LT3, LT5). Although these systemic problems hamper the realization of the social–ecological objectives, most companies continue to source from these countries for staying economically and technologically competitive.
Moreover, divergent learning elements are rooted in the economic system itself. Most companies struggled to achieve their social–ecological objectives because of the structural complexity of SCs (Learn4). Two interviewees noted that the complex SC structure is the main challenge in ensuring and improving the social–ecological performance of suppliers (TT3, TT4). However, the SC complexity also creates difficulties for suppliers themselves. Their social–ecological efforts are hardly recognized and valued by downstream SC members because of the non-visibility of their organizations and products (MT2, LT1, LT3, TP2).
Smaller companies reported that the economic system favoring large-scale producers (Learn2) is a divergent element for them. These companies struggled with having limited purchasing power, and thus, limited influence on their suppliers' sustainability (e.g. TT3, TT5, MT1, MT5). One managing director noted: “I often cannot put any demands and claims on them, since they would say […] If that does not suit you, you start searching from where you can get your stuff” (MT5).
Finally, we identified the absence of suitable standards and certifications (Learn3) conflicting with the realization of social–ecological objectives. Many managers emphasized standards and certifications as effective instruments for implementing social-ecological sustainability into SCs. In particular, lower-tier firms struggled with the nonavailability of suitable sustainability standards for ensuring the responsible sourcing of certain minerals (e.g. tungsten) (LT2, LT3, LT5, TP2).
4.1.2 Belonging elements
Belonging elements represent the divergent perspectives and views opposed to the social–ecological objectives in SC contexts.
The results showed that the suppliers' divergent understanding and perspectives (Belong1) are often sources of belonging elements of sustainability tensions. Especially smaller suppliers in the Global South often hold divergent perspectives on social–ecological topics because of a lack of sustainability awareness. One manager explained: “It must be kept in mind that everything we Europeans intend to do encounters different cultural circumstances and realities. And things that we approve [… not] everybody agrees with” (MT3). The divergent perspectives of suppliers not only complicate the implementation of sustainability measures (e.g. TT1, TT3, LT1, TP3) but also create problems in ensuring sustainability requirements in SCs (e.g. TT1, TT2, MT3, MT8).
The workers' acceptance of regulations and sustainability measures (Belong4) in the Global South was identified as another belonging element clashing with the realization of the social–ecological objectives. The results indicated that the perspectives of workers are strongly influenced by the socioeconomic environment in the Global South. Some companies faced the challenge of preventing extensive workhours in production facilities and mines of suppliers, as workers sought to maximize their income by disrespecting overtime restrictions (TT1, MT3, MT4).
Besides the upstream SC, belonging elements also arise from the industrial customers' sustainability requirements and expectations (Belong2). The social–ecological goals of companies often diverge from the sustainability expectations of industrial customers, which “restrict their focus on minimum standards” (MT3). This results in difficulties for companies to receive financial compensation and other forms of support for realizing their social–ecological goals – especially when their products and components have little visibility in the final product (e.g. MT2, MT3, MT7, LT1).
Finally, the sustainability expectations of end-customers (Belong3) result in the challenge of selling sustainable products when these products do not match the sustainability expectations of the end-customers. One top-tier firm (TT1) had end-customers who lacked awareness about the complexities and challenges regarding the management of social–ecological sustainability in SCs. A manager of the company explained that they need to be honest about the complexities related to sustainability and be humble about the possible changes, which “is not always easy from a marketing perspective, [since they] make claims that are a little bit more costly to understand because they require more understanding.”
4.1.3 Organizing elements
Organizing elements represent structures and processes competing with the means and ends of the desired social–ecological objectives in SC contexts.
The results showed that the design of standards and certifications (Organ1) can be an organizing element divergent from the realization of social–ecological goals. In our study, particularly smaller SC members struggled to join common standards and certifications because of their requirements or entry fees (TT2, TP2, TP3). For instance, the unintended consequences of certain mining standards were the exclusion and further marginalization of artisanal and small-scale miners in the Global South. One interviewee noted: “The problem is that all certification systems […] are mainly suitable for larger operations […] that can meet the requirements and have the opportunity to participate. And the smallest […] they cannot achieve those requirements. But they are the ones that actually need the support” (TP3).
Moreover, mid-tier firms faced sustainability tensions stemming from the varying measures and requirements of industrial customers (Organ2). Some interviewees noted the challenge of complying with the often varying social–ecological requirements and objectives of industrial customers (TT4, TT6, MT4, TP2). They explained that “each OEM [Original Equipment Manufacturer] has a different questionnaire and wants information about different things and different standards” (TT6), which causes difficulties in deploying all standards (MT4).
The current business operations and commercial decisions (Organ3) were also identified as a belonging element against the social–ecological goals needed to be implemented. This element often emerges from the dependency on other SC members, which influence the extent to which social–ecological objectives can be implemented into organizational and SC structures. Some mid-tier firms held on to their traditional processes and structures because of the low demands for (more) sustainable products (MT2, MT6). Other companies struggle with the problem of having only limited sustainable sources of primary materials and intermediates, which is why they need to fall back on traditional sources that do not match their social–ecological objectives (TT3, LT2, LT3).
The final organizing element identified is the logic of economic competition (Organ4). Although several managers viewed collaborations as important and necessary to realize their social–ecological objectives on a wider scale, their actions and measures followed the logic of competition (TT1, LT1, LT2, TP2). Especially lower-tier firms strove for competitive advantages by searching and developing ethical sources of primary materials, which in turn led to hesitations regarding collaborations with competitors on social–ecological topics.
4.1.4 Economic performing elements
Economic performing elements represent the economic objectives and goals that diverge from the implementation of social–ecological objectives in SCs.
The results showed that social–ecological sustainability often needs to be realized against the fundamental economic performing element of profit maximization (Perform3). Most companies faced additional costs when engaging in social–ecological measures, which naturally increase the prices of products and services (e.g. TT5, MT6, MT8, LT5). In particular, companies with low SC visibility struggled with selling products based on their social–ecological performance (MT3, LT4). One manager explained: “[…] contrary to what can probably be said about Fairtrade coffee, we cannot sell at higher prices” (MT3).
Another divergent economic performing element is minimizing risks (Perform4), which mostly conflicts with the objective of integrating disadvantaged producers and regions into the global market (e.g. LT1, LT2, LT5, TP4). The small and fluctuating outputs of artisanal and small-scale miners and the underlying systemic problems resulted in a higher exposure to reputational risks. However, several interviewees noted that boycotts of certain regions and producers would not only withhold the prospects for economic development but also drive the illegal sales of minerals in high-risk countries. One manager explained: “If the major brand or major sectors step out to avoid any reputational risk, […] this brings precious metals and all the other minerals into the illegal market” (LT2).
Ensuring competitive advantages and corporate secrets (Perform1) was also identified as an economic performing element. Some interviewees noted that suppliers are often reluctant, or even unwilling, to share information necessary for the implementation of social–ecological sustainability into SCs (e.g. TT1, TT2, TT3, TT5). In particular, the traceability of primary materials conflicts with this economic performing element. One company (TT3) reported that moving along the SC for “determining the names of sub-sub-suppliers in order to persuade them to buy fair minerals” represents a bigger challenge than finding ethical sources of minerals.
Finally, the meeting of customer demands (Perform2) was identified as an economic performing element that specifically diverges from the social–ecological objective of producing long-lasting products. Two top-tier firms (TT1, TT2) reported the challenge of convincing their customers to use their sustainably designed products over the long term until a technological point is reached, “where it makes sense to get a new device” (TT2).
4.1.5 Relationships between tensions and divergent elements
While the previous section analyzed the individual tensions, this section analyzes the sustainability tensions from an outside-in perspective by focusing on the relationship between tensions and their embeddedness in the larger SC context. By generalizing the level of emergence of the tension elements outlined in Table 3, a hierarchical structure among the tensions and paradoxes in SC contexts becomes evident.
Figure 3 illustrates the relationships among sustainability tensions and their levels of emergence in SC contexts by labeling the tensions according to the divergent elements (belonging, learning, organizing, and economic performing), which conflict with the realization of social–ecological goals. Learning elements emerge at the highest levels in SC contexts (“systemic” and “SC”) and influence the other divergent elements. Belonging elements appear exclusively at the “SC” level and influence the organizing and performing elements. Organizing and performing elements mutually influence each other and typically arise at the lowest levels in SC contexts (“SC” and “organizational”).
The relationship and influence of sustainability tensions with their divergent elements (opposed to the implementation of social–ecological sustainability in SCs) can be classified into six relationships (Figure 3), which are outlined in Table 4. In addition, Figure 3 shows how the interconnectedness of sustainability tensions and their divergent elements can result in a reinforcement of paradoxes. The interconnectedness of tensions has also been addressed in previous paradox literature (e.g. Schad et al., 2016).
4.2 Management strategies for responding to sustainability tensions
This section presents the most notable strategic responses to the sustainability tensions identified in our case study. We outline the specific practices used as response strategies to the divergent elements, which conflict with the realization of social–ecological objectives. Table 3 (outer right column) presents a complete overview of the identified practices used as response strategies for sustainability tensions. The results revealed that different sustainability tensions can be addressed by the same response practices, which can be attributable to the interconnectedness of the sustainability tensions.
4.2.1 Response practices used as contextualization strategy
Across almost all companies in our study, contextualization was identified as a common way of responding to the various sustainability tensions.
In particular, sustainability tensions emerging from learning elements often appear to be contextualized by organizations and their managers. Besides responding to the structural complexity of SCs (Learn4) opposed to social–ecological sustainability (e.g. TT3, TT4, TT5), internal contextualization (RP12) was applied for responding to the sustainability tension stemming from the systemic problems in the production countries (Learn1) of the Global South (e.g. TT1, MT3, LT1): “[…] we are doing everything possible and we are pleased about every success which we achieve, but we also have to handle failures” (MT3). Additionally, external contextualization (R11) was used to alleviate the sustainability tensions resulting from both Learn4 and Learn1. Some companies contextualized these conflicting elements to different stakeholder groups to make the related sustainability tensions more workable (e.g. TT1, TT3, TT4). Moreover, managers of small(er) companies used internal contextualization (RP12) to respond to the challenge of having limited influence in SCs stemming from the economic system favoring large-scale producers (Learn2) (TT1, TT2, MT5).
Regarding the economic performing elements, companies often contextualized the sustainability tensions emerging from the objectives of minimizing risks (Perform4) and profit maximization (Perform3). As a response to the conflicting economic objective of minimizing risks (Perform4), some lower-tier firms used external contextualization (RP11) to explain their intention to source from disadvantaged producers and regions to their industrial customers and pressure groups (LT1, LT2, LT3, LT5): “We said to them, look, we are going to build a mine here [in the Democratic Republic of the Congo] and we would be interested to know if you would take our material or not. And they said sure, […] we just had to make sure it complies with whatever reporting regulations are enforced at the time. And we said, we do not see that as a problem at all” (LT5). Sustainability tensions stemming from profit maximization (Perform3) were addressed through both internal contextualization (RP12) (TT1, TT2, MT2, LT3) and external contextualization (RP11) (TT1, MT3, MT4, LT2).
Finally, sustainability tensions emerging from belonging and organizing elements were found to be less frequently contextualized than the other categories of divergent elements. For instance, internal contextualization (RP12) and external contextualization (RP11) were both used for responding to the industrial customers' sustainability requirements and expectations (Belong2) (e.g. MT3, LT1), whereas only internal contextualization (RP12) was used for responding to the suppliers' divergent understanding and perspectives (Belong1) (TT1, TT3, MT3). Regarding sustainability tensions from divergent organizing elements, internal contextualization (RP12) was mostly found as a response to the need to maintain the current business operations and commercial decisions (Organ3) (TT3, MT2, LT3). For instance, some organizations considered the limited availability of sustainable sources when having to source materials not completely matching their social–ecological objectives (TT3, LT3). To cope with the organizing element of varying measures and requirements of industrial customers (Organ2), one mid-tier firm used external contextualization (RP11) to address the challenges of complying with all sustainability standards of industrial customers (MT4).
4.2.2 Response practices used as resolution strategies of separation and synthesis
4.2.2.1 Response practices as resolution strategies of separation
Most identified separation strategies used for responding to sustainability tensions can be categorized as spatial separation, which addresses tension elements at different locations or contextual levels.
Among the identified practices addressing learning elements, strategic business alliances (RP10) were used for realizing social–ecological objectives at a larger systemic level. For instance, some companies participated in these alliances to work on sourcing guidelines and sustainability standards in the industry (e.g. TT6, MT4), which addresses the sustainability tensions stemming from the structural complexity of SCs (Learn4). Regarding the problem of conflicting minerals in multi-tier SCs, one manager (MT4) explained: “You just cannot do that on your own, even as a multinational [enterprise].” For responding to systemic problems in producing countries (Learn1), companies joined public–private partnerships (RP09) to tackle systemic issues (TT4, TT6, LT2), like the formalization of artisanal and small-scale miners in South America (LT2). Smaller companies sought to increase their purchasing power and influence in SCs through long-term organizational growth (RP17) to address the sustainability tensions stemming from the economic system favoring large-scale producers (Learn2) (TT1, TT2, TT3).
Regarding the sustainability tensions stemming from organizing elements, one company joined a public–private partnership (RP09), which supports disadvantaged producers in meeting the design of standards and certifications (Organ1) (LT2). To cope with the varying measures and requirements of industrial customers (Organ2), some companies drove industry certifications and standards (RP02) together with other parties (including their industrial customers) in strategic business alliances (RP10) (TT4, TT6, MT4). The sustainability tensions stemming from the current business operations and commercial decisions (Organ3) were addressed through offering conventional and (more) sustainable products (RP23) for meeting the different (and potentially changing) expectations of industrial customers (MT2, MT6, LT2, LT3). Finally, some organizations responded to the sustainability tensions emerging from economic competition (Organ4) by collaborating with competitors in strategic business alliances (RP10) but only when having to address larger systemic issues (LT1, LT2).
Turning to the separation strategies for the economic performing elements, lower-tier firms were found to engage in strategic business alliances (RP10) and public–private partnerships (RP09) to address the divergent element of minimizing risks (Perform4) at a larger systemic level. These response practices were used to tackle the reputational and supply risks related to the sourcing of minerals from disadvantaged producers and regions (LT1, LT2). The reluctancy of suppliers to share information for protecting their competitive advantages and corporate secrets (Perform1) was, for example, addressed through continuous attempts to gradually increase transparency (RP19) in multi-tier SCs (TT2, TT3, TT5). To respond to the sustainability tensions stemming from profit maximization (Perform3), some companies used practices to reduce their individual efforts and expenses for ensuring sustainability in SCs. For instance, they drove industry-wide sustainability requirements and standards through strategic business alliances (RP10) (MT4, LT2) and engaged in the selective monitoring and controlling (RP04) of multi-tier SCs (e.g. based on the risk potential of suppliers) (TT1, LT2).
In our study, the only belonging element addressed through separation was the suppliers' divergent understanding and perspectives (Belong1). To realize their social–ecological objectives, some companies aimed for long-term relationships (RP14) with suppliers to gradually work on their sustainability understanding and performance (TT1, TT2, TT3, LT1).
4.2.2.2 Response practices used as resolution strategies of synthesis
Various synthesis strategies were used for responding to learning elements. Some companies engaged in supplier selection (RP07) based on certifications and standards (RP02) and other criteria to address the sustainability tensions emerging from the systemic problems in producing countries (Learn1) (e.g. TT4, MT4, LT3). One manager explained: “[…] we accept that suppliers can still be excellent in more difficult countries [… but] you have to upload certificates” (TT4). Moreover, certifications and standards (RP02) were used to address the structural complexity of SCs (Learn4) (e.g. TT6, MT5, LT4). For instance, documents were passed along companies in multi-tier SCs to ensure the conflict-freeness of minerals and products. In cases where the absence of suitable standards and certifications (Learn3) resulted in sustainability tensions, some companies established self-defined certifications and standards (RP02) (LT5, LT2). To deal with the economic system favoring large-scale producers (Learn2), small(er) companies sought to build long-term relationships (RP14) with suppliers to increase their influence over them, thereby compensating for their small purchasing volumes (TT3, MT2).
To address the belonging elements, companies engaged in different activities with the aim of aligning the divergent perspectives in SCs with their social–ecological objectives. For example, some companies responded to the sustainability tensions stemming from the industrial customers' sustainability requirements and expectations (Belong2) by raising the sustainability awareness (RP15) of their industrial customers. This was typically done for receiving some form of support for social–ecological goals and actions (MT3, MT6, LT1, LT3). While larger companies provided trainings and workshops to suppliers for addressing the suppliers' divergent understanding and perspectives (Belong1) (e.g. TT4, TT6), smaller companies sought personal contact to raise the sustainability awareness (RP15) of their suppliers for letting “them know what sustainability is and the importance of it” (TT1). To align the workers' acceptance of regulations and sustainability measures (Belong4) with its social–ecological objectives, one company implemented corporate social programs (RP22) designed for migrant workers in China to address the high employee turnover and the workers' motivation to engage in extensive overtime (MT3). Another company provided educational trainings to mining workers to raise the sustainability awareness (RP15) of them (TT1).
Furthermore, few synthesis strategies were identified to address the organizing elements. To respond to the sustainability tensions stemming from the current business operations and commercial decisions (Organ3), some companies sought to raise the sustainability awareness (RP15) of industrial customers to increase the demand (and orders) of sustainable products (e.g. MT2, MT6). To cope with the varying measures and requirements of industrial customers (Organ2), one company committed itself to widely accepted certifications and standards (RP02) for meeting the sustainability expectations of as many industrial customers as possible (MT4).
Turning to the synthesis strategies for economic performing elements, some companies addressed the sustainability tensions stemming from profit maximization (Perform3) through certifications and standards (RP02), which reduced the organizational efforts and expenses for ensuring social–ecological requirements (TT4, MT4, LT3). For the same reasons, some organizations engaged in supplier selection (RP07) to choose suppliers in low-risk countries (TT3, TT4), where it can be assumed “that the working standards comply with certain norms without the need for special agreements and checks” (TT3). By raising the sustainability awareness (RP15) of industrial customers (e.g. MT3, LT2, LT3) and engaging in industrial customer selection (RP21) (MT6, LT3), some companies sought to obtain financial compensation for their social–ecological efforts. To address the sustainability tensions emerging from minimizing risks (Perform4), some companies engaged in supplier development (RP06) and the monitoring and controlling (RP04) of disadvantaged producers that are associated with high risks (LT1, LT2). Finally, the sustainability tensions stemming from meeting of customer demands (Perform2) were addressed by offering technologically upgradable products (RP24) and raising the sustainability awareness (RP15) of the end-customers through sustainability campaigns (TT1, TT2).
5. Discussion
5.1 Theoretical contributions
Our study makes several contributions to the literature. The study deviates from the traditional “win-win” and “trade-off” perspectives on sustainability tensions by adopting a paradox perspective. Thereby, it answers calls for more empirical research on paradoxical sustainability tensions (e.g. Van der Byl and Slawinski, 2015), and particularly in SC contexts (e.g. Brix-Asala et al., 2018; Matthews et al., 2016; Xiao et al., 2019). Moreover, we identify underlying paradoxical sustainability tensions in SC contexts and reveal their relationships and influence among each other. The research studies the electronics SC context because of the high complexity that needs to be overcome when responding to sustainability tensions and paradoxes. In contrast to other empirical studies that focus on a single paradox (e.g. Wilhelm and Sydow, 2018; Xiao et al., 2019), this study adopts an outside-in perspective by focusing on the larger SC contexts to unveil multiple paradoxical sustainability tensions. While this approach may provide fewer details than studies focusing on individual paradoxes, our research provides valuable insights into the relationships among sustainability tensions. The findings indicate a hierarchical structure among tensions and paradoxes (Figure 3). The sustainability tensions emerging at higher levels have the potential to reinforce tension at lower levels in SC contexts.
Furthermore, the study provides insights into how companies in the electronic SC respond to paradoxical tensions in the form of SSCM practices. To synthesize these practices according to paradox response strategies, we build on previous concepts by incorporating the contextualization strategy found by Xiao et al. (2019) into the acceptance-resolution management cycle proposed by Hahn et al. (2015) (Figure 2). While other studies unveiling multiple sources of paradoxes neglected the identification of paradox strategies (Sandberg, 2017; Zhang et al., 2021), our study shows that many practices can address various paradoxical tensions simultaneously (Table 3), which can be explained by the interconnectedness of tensions. For example, certifications and standards (RP02) address the sustainability tensions stemming from the economic performing element of profit maximization (Perform3) and the learning element of structural complexity of SCs (Learn4). Similar to Xiao et al. (2019), our findings also emphasize the importance of contextualizing as a response strategy to paradoxical tensions. We show that companies can alleviate paradoxical sustainability tensions through both internal and external contextualization. Contextualization is particularly useful when the underlying causes of tensions and paradoxes are rooted in the larger levels of SC contexts, such as the systemic problems in producing countries (Learn1).
Building upon the multi-tier sampling logic in this case study, the empirical results enlarge the scarce SSCM literature on paradoxical tensions (Zhang et al., 2021) that has predominantly focused on single organizations (e.g. Brix-Asala et al., 2018; Xiao et al., 2019). Although our study primarily focuses on the context levels (Figure 1) for analyzing the origins of sustainability tensions in the electronics SC, it also provides evidence for the practicality of a multi-tier perspective. We show that social–ecological objectives and their divergent elements vary along the tiers of SCs (Table 3). For example, while upstream firms might aim for the integration of disadvantaged producers and regions that are associated with social–ecological misconduct (e.g. artisanal or small-scale miners in the Global South), downstream buying firms might intend to boycott the same producers and region for ensuring the minimum sustainability performance of the multi-tier SC. Paradoxical tensions can vary depending on the location of companies in SCs, and therefore, require different response strategies and practices. This supports previous multi-tier SSCM research by underlining the challenges and also the opportunities related to adopting a multi-tier focus for managing SCs (Mena et al., 2013; Tachizawa and Wong, 2014). Our findings also underline that successful SSCM depends on a comprehensive investigation of the SC levels in conjunction with the system (or context) in which companies are embedded (Sauer and Seuring, 2018).
5.2 Managerial implications
Our study provides several practical insights and managerial implications. First, managers are generally advised to understand the characteristics of tensions and their divergent elements by considering the entire system (or context). Once the divergent elements are identified and framed as paradoxical tensions, managers can rely on the strategies outlined in Figure 2 and the empirically identified practices in Table 3 to develop more targeted responses to sustainability tensions. This is in line with the call of other scholars to identify real-world paradoxes and responses (e.g. Van der Byl and Slawinski, 2015). Our results suggest that addressing the divergent elements of sustainability tensions (or paradoxes) at larger levels can alleviate the tensions at lower levels. However, divergent tension elements at higher levels are typically more difficult to address (e.g. systemic problems in producing countries, Learn1). Therefore, business alliances and other collaborations with third parties might play a crucial role in addressing the larger problems and complexities in SC contexts, leading to sustainability tensions. At least to some extent, the contextualization strategy helps to create flexibility for responding to sustainability tensions and paradoxes by generating the necessary leeway for companies (see also Xiao et al., 2019).
By indicating which strategies and practices have been successfully applied, we offer practical examples for managers on how to approach sustainability tensions. Even though our study focuses on the electronics SC only, the results offer insights for managers from other industries as well. The identified practices underline that many lower-tier and mid-tier firms actively engage in the management of social–ecological sustainability and their potential willingness to cooperate. Contextualization can be a key facilitator for multi-tier SC cooperations. Instead of insisting on their demands and requirements, it is essential that top-tier firms (or buying firms) understand how these demands influence upstream SC members (Sauer and Seuring, 2018). As the social–ecological objectives and challenges differ among SC tiers, managers are generally advised to consider the roles and positions of their companies in multi-tier SCs to understand the causes of paradoxical tensions and the related strategies.
6. Conclusion
Engaging in SSCM requires responding to sustainability tensions emerging from various activities and elements in wider SC contexts, which conflict with the realization of social–ecological outcomes. By applying a paradox perspective, our single case study presents sustainability tensions emerging in the global electronics SC contexts and practices used for responding to them. The findings indicate a hierarchal structure among sustainability tensions and emphasize the importance of contextualization when facing conflicting elements at higher context levels.
However, several limitations must also be addressed. Despite being specifically designed to reveal paradoxical sustainability tensions in multi-tier SC contexts, the interview guide did not comprise questions that explicitly ask for “tensions” or “paradoxes”. This leads to the limitations that the sustainability tensions might not be perceived as such by the interviewees and studied organizations, since the authors frame the social–ecological objectives with their conflicting elements as paradoxical tension. However, paradoxical tensions can be latent and grounded in the larger system (or context), even if actors may not cognitively perceive them as such (Schad and Bansal, 2018). Therefore, our methodological approach can be viewed as reasonable, particularly for revealing underlying paradoxical sustainability tensions within wider SC contexts.
Despite several attempts made to address this issue through snowball sampling, the identified tensions may lack some contextual depth because not all companies and third parties in the sample have a direct relationship with one of the other organizations in this study. Moreover, our study neglects the individual level as a source of paradoxical sustainability tensions (e.g. Xiao et al., 2019) and has a strong Eurocentric bias, which stems from the data sample mostly comprising of companies and third parties from the Global North. Although many of the identified sustainability tensions and response strategies can probably be generalized to other SC contexts, the focus on the electronics SC might represent another limitation.
Considering the results and limitations of this study, the following research directions can be derived. First, besides studying other SC contexts (e.g. food or textile SCs), future research could conduct in-depth analyses of the identified sustainability tensions and response strategies outlined in this study. In addition, future research could focus on a reduced set of companies, which can be guided by the context levels (e.g. “systemic”) and/or the management response strategies (e.g. “synthesis”). Moreover, researchers could focus on the specific relationships of paradoxical sustainability tensions (e.g. organizing and economic performing) or the different transitions of the virtuous cycle for responding to them.
Second, Eurocentric biases can be overcome by including more companies from the Global South to capture their perspectives and contextual influences. This can help to reveal the challenges and tensions faced by suppliers when dealing with the sustainability expectations of the Global North. As empirical evidence in SSCM research is largely missing (Zhang et al., 2021), more qualitative studies on paradoxes and their management are required to gain contextual depth. Our research can also help to operationalize tensions and paradoxes in SC contexts, which can open up avenues for empirical–quantitative research. For example, future studies could investigate the occurrence and severity of (paradoxical) tensions across different contexts or quantify the influence of certain practices on tensions, thereby moving toward their prioritization.
Third, although we applied a multi-tier sampling strategy, we could not fully realize an analysis of the multi-tier SC aspects. However, this could yield valuable insights into the context of sustainability tensions through the investigation of relationships between members in multi-tier SCs. Our study shows that sustainability tensions and their divergent elements can differ along multi-tier SCs and might require different responses. For instance, future studies could focus on triads in SCs (e.g. Mena et al., 2013) to explore the complexities and dynamics resulting in tension and paradoxical situations.
Figures
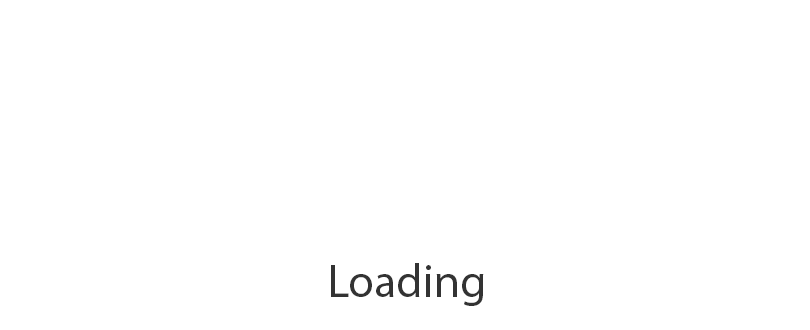
Figure 1
Amended framework for categorizing sustainability tensions in SC contexts based on Hahn et al. (2015) and Smith and Lewis (2011)
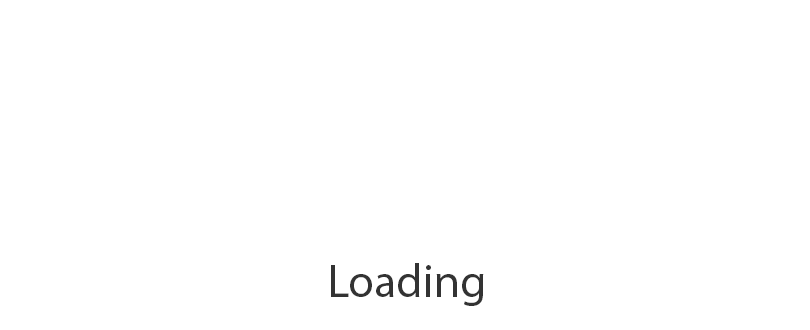
Figure 2
Adapted response cycle for sustainability tensions based on Hahn et al. (2015)
Main sources of sustainability tensions in supply chain contexts
Main sources of sustainability tensions |
---|
Learning tensions emerge when “dynamic systems change, renew, and innovate” (Smith and Lewis, 2011, p. 383). For ensuring their long-term sustainability, most systems need to be built upon (and destroy) the old system for creating opportunities and/or adopt to the future. Learning tensions and paradoxes usually surface during the times of transition and change. The tensions can be simply described as “old vs. new,” “stability vs. change,” and “present vs. future” (Schad et al., 2016). As sustainable development requires shifts to (more) sustainable business practices, learning tensions are omnipresent in sustainable SC contexts. Learning tensions and paradoxes usually emerge “between the need to radically depart from currently unsustainable [or insufficiently sustainable] business practices and products and the need to build upon existing routines and systems” (Hahn et al., 2018, p. 237) |
Belonging tensions are driven by the different and often divergent identities, values, and views of actors in specific contexts (Smith and Lewis, 2011). These tensions typically arise between the individual and the collective, as well as within and across organizations in SCs (Schad et al., 2016). As sustainable development is an inherently normative concept (Gold and Schleper, 2017; Hahn et al., 2018), belonging tensions and related paradoxes commonly surface between individuals and/or organizations holding different values and views about social and environmental sustainability (Hahn et al., 2018). Often, belonging tensions and paradoxes become even more salient in global sourcing contexts due to cultural differences and divergent perspectives (Sandberg, 2017). As individuals and organizations define goals based on their identity and believes, belonging tensions can be viewed as underpinnings of performing tensions (Mason and Doherty, 2016) |
Organizing tensions surface when organizations and SCs create competing structures and processes to achieve desired outcomes (Smith and Lewis, 2011). These tensions emerge from difficulties in determining and establishing appropriate methods for particular purposes. Organizing tensions and paradoxes often manifest themselves as conflicts between “empowerment vs. control” (Mason and Doherty, 2016), “cooperation vs. competition” (i.e. coopetition) (Manzhynski and Figge, 2020; Wilhelm and Sydow, 2018), and “integrate vs. separate” (Smith and Lewis, 2011; Sandberg, 2017). The integration of social–ecological sustainability into the core business structures and processes often leads to the emergence of organizing tensions. Organizing paradoxes typically arise from the need to fully integrate sustainability activities into the core business operations, while having to follow and maintain a commercial business logic (Hahn et al., 2018) |
Performing tensions stem from the plurality and variety of goals, which are typically imposed by the demands and expectations of internal and external stakeholders. Performing tensions usually emerge within and between organizations in SC contexts when the simultaneously pursued goals and strategies conflict with each other (Smith and Lewis, 2011). With regards to sustainable development and corporate sustainability, performing tensions are often portrayed and operationalized through the three dimensions of the triple bottom line: social, environmental, and economic sustainability. The related tensions and paradoxes usually emerge from the need to simultaneously address social, environmental, and economic goals that often reside in the present and future (Hahn et al., 2015; Slawinski and Bansal, 2015). Performing tension and the related paradoxes “touch the very heart of corporate sustainability and its ambition to contribute to a diverse set of potentially competing sustainability issues” (Hahn et al., 2018, p. 238) |
Firms and third-party organizations in the case study
Actors | SC position/role1 | Main products | Employees | Turnover | Size | Location of headquarter | Role of interviewee(s)2 | Secondary material |
---|---|---|---|---|---|---|---|---|
TT1 | Top-tier firm | Smartphones | 11–100 | € 11–25 million | Medium | Europe |
| Blog, webpage |
TT2 | Top-tier firm | Smartphones | <10 | <€ 5 million | Small | Europe |
| Sustainability report, webpage |
TT3 | Top-tier firm | Computer mouse | <10 | <€ 5 million | Small | Europe | [No interview]3 | Blog, newsletter, webpage |
TT4 | Top-tier firm | Electronic vehicles | >501 | >€ 1 billion | Large | Europe |
| Sustainability report, webpage |
TT5 | Top-tier firm | Electronic vehicles | <10 | >€ 5 million | Small | Europe |
| Blog, webpage |
TT6 | Top-tier firm | Electronic vehicles | >501 | >€ 1 billion | Large | Europe |
| Corporate report, webpage |
MT1 | Mid-tier firm | Assembly services | 11–100 | n.a | Small | Europe |
| Webpage |
MT2 | Mid-tier firm | Coatings for electronics | 101–500 | € 11–25 million | Medium | Europe |
| Webpage |
MT3 | Mid-tier firm | Connectors and cables | 101–500 | € 26–50 million | Medium | Europe |
| Flyer, webpage |
MT4 | Mid-tier firm | Semiconductors | >501 | >€ 1 billion | Large | Europe |
| Sustainability report, webpage |
MT5 | Mid-tier firm | Capacitors | 11–100 | € 5–10 million | Small | Europe |
| Webpage |
MT6 | Mid-tier firm | Plastic parts and components | 11–100 | € 5–10 million | Small | Europe |
| Blog, webpage |
MT7 | Mid-tier firm | Various intermediates for electronic vehicles | >501 | >€ 1 billion | Large | Europe |
| Sustainability report, webpage |
MT8 | Mid-tier firm | Various intermediates for electronic vehicles | >501 | >€ 1 billion | Large | Europe |
| Webpage |
MT9 | Mid-tier firm | Battery system for electronic vehicles | >501 | >€ 1 billion | Large | Europe |
| Webpage |
MT10 | Mid-tier firm | Printed circuit boards (PCBs) | >501 | € 500 million to 1 billion | Large | Europe |
| Webpage |
LT1 | Lower-tier firm | Tungsten smelter and refiner | 101–501 | € 26–50 million | Medium | Europe |
| Due diligence report, webpage |
LT2 | Lower-tier firm | Gold refiner | 101–501 | € 51–200 million | Medium | Europe |
| Sustainability report, webpage |
LT3 | Lower-tier firm | Solder (primarily out of tin) | 11–100 | € 26–50 million | Small | Europe |
| Webpage |
LT4 | Lower-tier firm | Tin | >501 | € 500 million to 1 billion | Large | South America |
| Corporate report, webpage |
LT5 | Lower-tier firm | Tungsten | 11–100 | € 26–50 million | Medium | Africa |
| Annual public report, webpage |
TP1 | Third-party organization (standard & certification) | n.a | n.a | n.a | n.a | South America |
| Webpage |
TP2 | Third-party organization (NGO4) | n.a | n.a | n.a | n.a | Europe |
| Webpage |
TP3 | Third-party organization (public-private partnership) | n.a | n.a | n.a | n.a | Europe |
| Webpage |
TP4 | Third-party organization (NGO) | n.a | n.a | n.a | n.a | Europe |
| Blog, webpage |
Note(s): 1Top-tier firms: Original equipment manufacturers located far downstream in the SC, with great public visibility and proximity to end-consumers; Mid-tier firms: Companies responsible for assembling and producing intermediates and final products; Lower-tier firms: Companies located far upstream in the SC, engaging in the trading, refining, and excavation of primary materials
2The two NGO members of TP2 were interviewed separately. Therefore, the single case study with 25 embedded units of analysis entails 25 semi-structured interviews, although no interview was conducted with TT3
3When being contacted to request an interview, the managing director of TT3 referred to the webpage and blog of the company, which are used to regularly communicate updates on sustainability measures, challenges, and shortcomings in their SC. The decision was made to include TT3 in the case study after a pre-assessment of the secondary material. Additional information about TT3 could be gathered through interviews with some companies (MT1, MT5, MT6, and LT3) in the data sample that are (sub-)suppliers of TT3
4Non-governmental organization (NGO)
Overview of identified sustainability tensions and response strategies
![]() |
![]() |
![]() |
Relationships among the divergent elements of sustainability tensions
Lable | Relationships among divergent element | Description |
---|---|---|
1 | Learning to economic performing | Learning tensions rooted in the routines and structures of the “systemic” (e.g. country and industry) and “SC” levels underpin the economic performing tensions emerging at the “organizational” and “SC” levels. For instance, the structural complexity of SCs (Learn4) strengthens divergent economic performing elements of profit maximization (Perform3) by driving the costs and efforts related to the implementation of social–ecological objectives. Another example is the systemic problems in producing countries (Learn1) that often drive the divergent economic performing element of minimizing risks (Perform4) when aiming to integrate disadvantaged producers in high-risk countries into SCs and the global market |
2 | Learning to belonging | Learning tensions erode the perceived relevance of social–ecological sustainability and related regulation. This, in turn, enables belonging tensions at the “SC” level. For instance, the learning element of systemic problems in producing countries (Learn1) leading to unenforced laws reinforces the divergent belonging element of workers' acceptance of regulations and sustainability measures (Belong4), as many workers are willing to work extensive hours to maximize their income. Present institutions (e.g. unenforced and/or weak laws) resulting in systemic problems in producing countries (Learn1) also reinforce the suppliers' divergent understanding and perspectives (Belong1) of social–ecological topics |
3 | Learning to organizing | Learning tensions underline organizing tensions at the “organizational” and “SC” levels. For instance, the structural complexity of SCs (Learn4) results in a low visibility of upstream firms (mid-tier and lower-tier firms) that struggle to depart from their current business operations and commercial decisions (Organ3), as their sustainability efforts are hardly recognized and valued by downstream SC members. Moreover, the structural complexity of SCs (Learn4) reinforces sustainability tensions stemming from the varying measures and requirements of industrial customers (Organ2), which are faced by many upstream firms in SCs |
4 | Belonging to organizing | Belonging tensions at the “SC” level can reinforce organizing tensions. For instance, the current business operations and commercial decisions (Organ3) of suppliers are reinforced when the industrial customers' sustainability requirements and expectations (Belong2) are limited to a minimum or the status quo. In contrast, the current business operations and commercial decisions (Organ3) of buyers can also be reinforced through the suppliers' divergent understanding and perspectives (Belong1) of social–ecological sustainability. This challenge is often faced by buying companies with low purchasing power or high dependency on certain suppliers |
5 | Belonging to economic performing | Belonging tensions can drive the emergence of economic performing tension. For instance, the suppliers' divergent understanding and perspectives (Belong1) of social–ecological topics and ways of doing business can reinforce the economic performing element of minimizing risks (Perform4). Suppliers that hold different sustainability perspectives (e.g. due to different contextual factors) increase the risk of sustainability misconducts. Moreover, the industrial customers' sustainability requirements and expectations (Belong2) can reinforce tensions related to the economic performing element of profit maximization (Perform3). Financial compensations for sustainability measures are difficult to achieve when industrial customers hold divergent expectations and views regarding social–ecological topics |
6 | Organizing to economic performing | There is a strong link between organizing and economic performing tensions, both of which emerge at the “organizational” and “SC” levels. For example, the varying measures and requirements of industrial customers (Organ2) increase the expenses of suppliers. This, in turn, strengthens the sustainability tension stemming from the divergent element of profit maximization (Perform3). Furthermore, profit maximization (Perform3) reinforces the organizing element of competition (Organ4). Instead of participating in collective actions to address social–ecological objectives on a larger scale, companies take individual actions to secure profits and competitive advantages with (more) sustainable products |
References
Brix-Asala, C., Geisbüsch, A.K., Sauer, P.C., Schöpflin, P. and Zehendner, A. (2018), “Sustainability tensions in supply chains: a case study of paradoxes and their management”, Sustainability (Switzerland), Vol. 10 No. 2, doi: 10.3390/su10020424.
Brix-Asala, C., Seuring, S., Sauer, P.C., Zehendner, A. and Schilling, L. (2021), “Resolving the base of the pyramid inclusion paradox through supplier development”, Business Strategy and the Environment, doi: 10.1002/bse.2798.
Carter, C.R., Rogers, D.S. and Choi, T.Y. (2015), “Toward the theory of the supply chain”, Journal of Supply Chain Management, Vol. 51 No. 2, pp. 89-97.
Carter, C.R., Kaufmann, L. and Ketchen, D.J. (2020), “Expect the unexpected: toward a theory of the unintended consequences of sustainable supply chain management”, International Journal of Operations and Production Management, Vol. 40 No. 12, pp. 1857-1871.
Eisenhardt, K.M. and Graebner, M.E. (2007), “Theory building from cases: opportunities and challenges”, Academy of Management Journal, Vol. 50 No. 1, pp. 25-32.
Ferraro, F., Etzion, D. and Gehman, J. (2015), “Tackling grand challenges pragmatically: robust action revisited”, Organization Studies, Vol. 36 No. 3, pp. 363-390.
Gioia, D.A., Corley, K.G. and Hamilton, A.L. (2013), “Seeking qualitative rigor in inductive research: notes on the Gioia methodology”, Organizational Research Methods, Vol. 16 No. 1, pp. 15-31.
Glover, J. (2020), “The dark side of sustainable dairy supply chains”, International Journal of Operations and Production Management, Vol. 40 No. 12, pp. 1801-1827.
Gold, S. and Schleper, M.C. (2017), “A pathway towards true sustainability: a recognition foundation of sustainable supply chain management”, European Management Journal, Vol. 35 No. 4, pp. 425-429.
Govindan, K., Shaw, M. and Majumdar, A. (2021), “Social sustainability tensions in multi-tier supply chain: a systematic literature review towards conceptual framework development”, Journal of Cleaner Production, Vol. 279, p. 123075.
Grimm, J.H., Hofstetter, J.S. and Sarkis, J. (2014), “Critical factors for sub-supplier management: a sustainable food supply chains perspective”, International Journal of Production Economics, Vol. 152, pp. 159-173.
Hahn, T., Pinkse, J., Preuss, L. and Figge, F. (2015), “Tensions in corporate sustainability: towards an integrative framework”, Journal of Business Ethics, Vol. 127 No. 2, pp. 297-316.
Hahn, T., Pinkse, J., Preuss, L. and Figge, F. (2016), “Ambidexterity for corporate social performance”, Organization Studies, Vol. 37 No. 2, pp. 213-235.
Hahn, T., Figge, F., Pinkse, J. and Preuss, L. (2018), “A paradox perspective on corporate sustainability: descriptive, instrumental, and normative aspects”, Journal of Business Ethics, Vol. 148 No. 2, pp. 235-248.
Hofmann, H., Schleper, M.C. and Blome, C. (2018), “Conflict minerals and supply chain due diligence: an exploratory study of multi-tier supply chains”, Journal of Business Ethics, Vol. 147 No. 1, pp. 115-141.
Lewis, M. (2000), “Exploring paradox: toward a more comprehensive guide”, The Academy of Management Review, Vol. 25 No. 4, pp. 760-776.
Manzhynski, S. and Figge, F. (2020), “Coopetition for sustainability: between organizational benefit and societal good”, Business Strategy and the Environment, Vol. 29 No. 3, pp. 827-837.
Mason, C. and Doherty, B. (2016), “A fair trade-off? Paradoxes in the governance of fair-trade social enterprises”, Journal of Business Ethics, Vol. 136 No. 3, pp. 451-469.
Matthews, L., Power, D., Touboulic, A. and Marques, L. (2016), “Building bridges: toward alternative theory of sustainable supply chain management”, Journal of Supply Chain Management, Vol. 52 No. 1, pp. 82-94.
Mena, C., Humphries, A. and Choi, T.Y. (2013), “Toward a theory of multi-tier supply chain management”, Journal of Supply Chain Management, Vol. 49 No. 2, pp. 58-77.
Poole, M.S. and van de Ven, A.H. (1989), “Using paradox to build management and organization theories”, Academy of Management Review, Vol. 14 No. 4, pp. 562-578.
Sandberg, E. (2017), “Introducing the paradox theory in logistics and SCM research–examples from a global sourcing context”, International Journal of Logistics Research and Applications, Vol. 20 No. 5, pp. 459-474.
Sauer, P.C. and Seuring, S. (2018), “A three-dimensional framework for multi-tier sustainable supply chain management”, Supply Chain Management: An International Journal, Vol. 23 No. 6, pp. 560-572.
Schad, J. and Bansal, P. (2018), “Seeing the forest and the trees: how a systems perspective informs paradox research”, Journal of Management Studies, Vol. 55 No. 8, pp. 1490-1506.
Schad, J., Lewis, M.W., Raisch, S. and Smith, W.K. (2016), “Paradox research in management science: looking back to move forward”, Academy of Management Annals, Vol. 10 No. 1, pp. 5-64.
Schmidt, C.G., Foerstl, K. and Schaltenbrand, B. (2017), “The supply chain position paradox: green practices and firm performance”, Journal of Supply Chain Management, Vol. 53 No. 1, pp. 3-25.
Slawinski, N. and Bansal, P. (2015), “Short on time: intertemporal tensions in business sustainability”, Organization Science, Vol. 26 No. 2, pp. 531-549.
Smith, W.K. and Lewis, M. (2011), “Toward a theory of paradox: a dynamic equilibrium model of organizing”, Academy of Management Review, Vol. 36 No. 2, pp. 381-403.
Smith, W.K. and Tracey, P. (2016), “Institutional complexity and paradox theory: complementarities of competing demands”, Strategic Organization, Vol. 14 No. 4, pp. 455-466.
Smith, W.K., Besharov, M.L., Wessels, A.K. and Chertok, M. (2012), “A paradoxical leadership model for social entrepreneurs: challenges, leadership skills, and pedagogical tools for managing social and commercial demands”, Academy of Management Learning and Education, Vol. 11 No. 3, pp. 463-478.
Tachizawa, E.M. and Wong, C.Y. (2014), “Towards a theory of multi-tier sustainable supply chains: a systematic literature review”, Supply Chain Management: An International Journal, Vol. 19, pp. 643-653.
Touboulic, A., Chicksand, D. and Walker, H. (2014), “Managing imbalanced supply chain relationships for sustainability: a power perspective”, Decision Sciences, Vol. 45 No. 4, pp. 577-619.
Van der Byl, C.A. and Slawinski, N. (2015), “Embracing tensions in corporate sustainability: a review of research from win-wins and trade-offs to paradoxes and beyond”, Organization and Environment, Vol. 28 No. 1, pp. 54-79.
Voss, C., Tsikriktsis, N. and Frohlich, M. (2002), “Case research in operations management”, International Journal of Operations and Production Management, Vol. 22 No. 2, pp. 195-219.
Wilhelm, M. and Sydow, J. (2018), “Managing coopetition in supplier networks – a paradox perspective”, Journal of Supply Chain Management, Vol. 54 No. 3, pp. 22-41.
Wu, Z. and Pagell, M. (2011), “Balancing priorities: decision-making in sustainable supply chain management”, Journal of Operations Management, Vol. 29 No. 6, pp. 577-590.
Xiao, C., Wilhelm, M., van der Vaart, T. and van Donk, D.P. (2019), “Inside the buying firm: exploring responses to paradoxical tensions in sustainable supply chain management”, Journal of Supply Chain Management, Vol. 55 No. 1, pp. 3-20.
Yin, R.K. (2014), Case Study Research: Design and Methods, 5th Ed., SAGE Publications, Thousand Oaks, CA.
Zhang, J., Yalcin, M.G. and Hales, D.N. (2021), “Elements of paradoxes in supply chain management literature: a systematic literature review”, International Journal of Production Economics, Vol. 232, p. 107928.
Acknowledgements
The authors would like to thank Lennart Endres and Philipp Spitzner for their contribution to the data collection. The authors also thank the guest editor, Pietro Micheli, and the two anonymous reviewers for their constructive comments and suggestions for improving the paper.