Abstract
Purpose
The purpose of this paper is to reach a deeper understanding of the Lean principle of respect for people (RFP to facilitate Lean implementation in Western organizations outside Toyota.
Design/methodology/approach
This study uses an interpretative, hermeneutic approach to understand the RFP concept through a literature study of existing research about Lean implementation, and an inquiry into the underlying meaning of the RFP principle, by studying sources from Toyota and discussions about the RFP principle in Japan.
Findings
RFP is seen as a central principle in Lean implementations, but the failure of RFP is believed to cause Lean implementations to fail. The literature about Lean discusses the RFP principle both as a general positive atmosphere and as focused on developing the work capacity of employees. By studying the sources from Toyota, it could be understood that RFP is based on ought-respect. The authors also find that RFP is related to takumi, a perfected form of craftsmanship. The authors translate the concept to English by tying it to the recent literature about craft to develop RFP as RFC – respect for craftsmanship.
Research limitations/implications
As this is a conceptual paper, it is difficult to translate the findings into a tool for companies and organizations to use. However, that is the point of the paper: that the most important ideas are not translatable into tools.
Practical implications
It is necessary in Lean implementations to connect people’s work to craftsmanship. Through a discussion of craftsmanship before Lean implementations, it might be possible to nurture an understanding of the underlying values of Lean.
Originality/value
The authors have not found any papers that propose takumi as the base of the RFP principle, nor as a foundational concept at Toyota. It is necessary to understand the concept of takumi, as perfection in craft, to understand the RFP principle.
Keywords
Citation
Ljungblom, M. and Lennerfors, T.T. (2021), "The Lean principle respect for people as respect for craftsmanship", International Journal of Lean Six Sigma, Vol. 12 No. 6, pp. 1209-1230. https://doi.org/10.1108/IJLSS-06-2020-0085
Publisher
:Emerald Publishing Limited
Copyright © 2019, Mia Ljungblom and Thomas Taro Lennerfors.
License
Published by Emerald Publishing Limited. This article is published under the Creative Commons Attribution (CC BY 4.0) license. Anyone may reproduce, distribute, translate and create derivative works of this article (for both commercial and non-commercial purposes), subject to full attribution to the original publication and authors. The full terms of this license may be seen at http://creativecommons.org/licences/by/4.0/legalcode
Introduction
Successful organizations are often characterized by an environment in which mutual respect prevails (Coetzee et al., 2019a; Liker and Hoseus, 2008; Marksberry, 2011). The Toyota Global Site (2020a, 2020b, 2020c, 2020d) states: “We respect others, make every effort to understand each other, take responsibility and do our best to build mutual trust” (Toyota Global Site, 2020a). With that in mind, Toyota’s successful management philosophy, The Toyota Way (a main source of inspiration for “Lean”), and its two principles Respect for people (RFP) and Continuous improvement (CI) can be a good choice when organizations want or need to improve. However, the success that Toyota has gained over the years is not easy to find elsewhere. After more than 20 years of adopting Lean, it is hard to find a single organization outside Toyota Corporation that has managed to improve its quality and reduce costs as much as Toyota (Rother, 2013). Research in the area has argued that fewer than 10% of companies succeed at implementing Lean practices (Belhadi et al., 2019; Cochran et al., 2012; Loh and Yusof, 2020). Based on the existing knowledge about the success of Toyota, it is clear that while fundamental knowledge of tools, techniques, technology and basic concepts is very important, an effective social environment in which people feel empowered and motivated is critical (Yadav et al., 2017). There is something that pervades Toyota’s thinking and culture that sets the company apart (Liker, 2004; Rother, 2013).
This naturally places the focus on the RFP principle. The existing literature states that the lack of RFP is one of the biggest reasons for the failure of Lean implementations in Western contexts (Coetzee et al., 2019a; Emiliani, 2009; Yadav et al., 2017). Although we have known about this missing component for more than a decade, there is still more failure than success in implementing Lean outside Toyota (Belhadi et al., 2019; Cochran et al., 2012; Loh and Yusof, 2020). Several researchers, such as Marksberry (2011), Emiliani (2009), Coetzee et al. (2019a) and Liker and Hoseus (2008), have stated that the RFP principle is the key to making the Lean system work.
Our research started from the idea that the lack of RFP is a major cause of failure in Lean implementations. Therefore, we were interested in understanding what RFP is and what it would mean to truly respect people in Lean implementations. Given that earlier research has shown that there is a deeper, cultural layer at stake (Liker, 2004; Rother, 2013), we also set out to understand what RFP means at Toyota in Japan, what concepts of respect and people are used at Toyota and how that understanding potentially differs from the principle as it is discussed in the research literature on Lean implementations.
The aim of the present study is to unveil the deeper, cultural layer that forms the basis of the RFP principle. In doing so, we intend to present an understanding of what RFP means that goes beyond current understandings in the studied literature.
Our research questions are as follows:
What is the meaning of RFP as defined in literature about RFP in Lean implementations?
What is the meaning of RFP as defined by Toyota and connected to the cultural context of Japan?
How can the RFP principle be accurately translated to other contexts?
Methodology
The methodology used in this article is loosely based on hermeneutics, which was originally developed to interpret texts. It is currently a widely used qualitative methodology within management and organization studies (Prasad and Prasad, 2002). Interpretive research is built upon the philosophy of social construction (Berger and Luckmann, 1966), which views social reality as constructed by people through meaningful interpretations.
The hermeneutic method is well-suited to the present study, given that our aim is to understand the concept of RFP. The hermeneutic method proposes that we shift perspectives linking the micro (which, in the present paper, means the RFP principle) with the macro, such as the cultural context in Japan, and use such shifts in perspective to increasingly reach a deeper understanding. When it comes to RFP, for example, one can read about how the concept is understood in some sources from Toyota and then relate it to the cultural context of Japan, then study what the Japanese concept of respect means in relation to the concept of respect in English. Through shifts of perspective, we can reach an additional understanding of the concept. In that sense, our methodology differs from a structured literature review, which is a methodological approach that has been applied to the study of RFP (Coetzee et al., 2019a). Although the hermeneutic approach can appear less structured, and thus less scientific, than a structured literature review it has great potential because it allows researchers to oscillate between a number of resources to create a more developed understanding of the concept. Although there is no conflict between a structured literature review and the hermeneutic method, the latter urges us to link the understanding of RFP in different texts to their context. The shifts of perspective used in our take on the hermeneutic method enable us to shift between three interrelated perspectives, which correspond to our research questions.
In relation to RQ1, we searched for the relevant scholarly articles about Lean and RFP written in English and from a geographical context other than Japan. The first author conducted two literature searches in Scopus during February 2020, referred to here as A and B. In literature search A the search terms Lean and RFP were used; in B, Lean and respect were used. Delimitations made were to the search after articles in English. This resulted in 22 hits in A and 1,349 in B. The first step in evaluating the articles was to read the abstracts to get information about whether the article discussed Lean with a focus on people in the organizations. The first author started to read the abstracts in A, with 22 hits between 2004 and 2019. All 22 articles were relevant, but the full versions of two of the 22 articles could not be found, so only 20 full articles were read. In B, after reading the first 253 abstracts (all from 2017 to 2020) of the 1,349 articles, the first author found that only 24 were about Lean. Only 10 of these 24 articles were relevant (focusing on Lean and people) and 7 had been found in the literature search A as well. Based on that poor result (only 1% new articles), the other articles in B were left unread. The final number of articles from the two literature searches was 23 articles. As a first way of analyzing the 23 articles, the first author classified them according to an evaluation sheet with criteria for evaluating the 23 articles (Appendix). The criteria for evaluating the articles were based on whether they explicitly dealt with RFP, defined it, discussed it and connected it to its cultural context. While reading the articles in the literature search, interesting references emerged, and those were also used as references in this paper.
In relation to RQ2, we analyzed the literature stemming from Toyota’s perspective on RFP, whether from managers at Toyota or researchers who have significant experience of Toyota. Concretely, this meant reading original sources from Toyota; that is, books written by former executives in the organization together with people who have influenced, worked at or studied at the organization. An example is Jeff Liker, who studied Toyota for more than two decades and was given unprecedented access to Toyota executives, employees and factories to gain a better understanding of the Toyota Production System (TPS) (Coetzee et al., 2019a). Another example is Mike Rother, who studied Toyota for six years (Rother and Arbor, 2014). We also studied the Toyota website, and although the second author has some Japanese language skills, we received help with the translation from (anonymized), a Japanese professor of business administration. To further contextualize, we conducted a search for an understanding of RFP, respect and people in Japan, opening the door to literature that is not directly related to Lean, to understand the broader context of the RFP principle. This was based on analyzing the RFP principle in Japanese, which helped us understand that they use a particular version of the word respect. This led to further investigations through literature searches and discussions with the above-mentioned professor. Furthermore, the RFP principle in Japanese also indicated a particular view of the concept of people. We also investigated the concepts of monozukuri, hitozukuri and kotozukuri. What we found to be most important, and not discussed in the earlier anglophone literature, is the concept of takumi – a perfected form of craftsmanship.
In relation to RQ3, we connected the understanding that we obtained from RQ2 to concepts similar to takumi in the West, but as we found none better than “a perfected form of craftsmanship”, we turned to the theoretical literature on crafts to facilitate a translation of takumi to the non-Japanese context.
Findings
What does respect for people mean in Lean literature?
According to the existing research in Western countries, the RFP principle has been almost entirely ignored in Lean implementations (Emiliani, 2009). Researchers such as Marksberry (2011), Emiliani (2009), Coetzee et al. (2019a) and Liker and Hoseus (2008) have stated that the RFP principle is the key to make the Lean system work. Indeed, 61% of the articles in the literature studies discussed RFP and 61% stated that the low result of Lean implementation success is due to the lack of RFP.
However, there was almost an exclusive focus on tools in Lean implementation. According to Yadav et al. (2017), the tools and methods used in Lean are the same basic tools and concepts used by every other organization or industry. In the same vein, VA Assen (2018) stated that the Lean tools represent at most 20% of the required effort in Lean transformations. The other 80% of the effort is expended on changing people’s practices and behaviors and, ultimately, their mindset. In a survey from 2009, 20% of the 515 respondents recognized changing the organizational culture as the biggest challenge that companies face (Traylor, 2011). Likert (2004) emphasized the special Lean culture: “The fundamental insight I have from my studies of Toyota is that its success derives from balancing the role of people in an organizational culture that expects and values their continuous improvements, with a technical system focused on high-value adds flow” (Likert, 2004, p. xv). Without the proper Lean culture, in which RFP is a central component, the Lean that is implemented can be called fake Lean (Bäckström and Ingelsson, 2016).
Developing this train of thought, Rother (2013) and Foley and Zahner (2009) argued that rather than focusing on the visible tools, we should instead try to understand the invisible routines of thought and action. As we mentioned in our introduction, a guiding thought in the present paper is that the invisible leadership routines of thought and action are related to a deeper, cultural layer. (Figure 1 shows a comparison between Rother’s model and ours.)
According to this idea of Lean implementation, organizations that have failed to implement Lean have used tools built on a specific cultural practice built up at Toyota, which is probably linked to Japanese culture, but does not make these cultural assumptions explicit. While it was known 15 years ago that tools and methods are not enough to reach success, Lean implementations with a clear focus on tools still seem to proliferate. Lean is still an add-on tool in the West, where the managerial culture and the employee’s engagement are missing (Kusy et al.2015). A possible reason for this is that Lean literature does not clearly define RFP.
When reviewing the articles about RFP, we found that the definitions of RFP are diverse and point in different directions. Researchers of Lean use different definitions of respect.
Two extremes of definitions of RFP can be found in the reviewed Lean literature. One extreme is represented by Womack’s (2008) definition:
“Only by showing mutual respect – each for the others and for each other’s role – is it possible to solve problems, make work more satisfying and take organizational performance to an even higher level” (p. 1).
Here, RFP is the underlying organizational atmosphere that allows for effective problem solving and increasing organizational performance. A similar definition can be found in Oppenheim et al. (2009):
“Respect People: A Lean enterprise is an organization that recognizes that its people are the most important resource and is one which adopts high performance work practices. In a Lean enterprise people brainstorm openly without fear, plan together by consensus, identify problems honestly, and solve problems in real time effectively, not allowing the problem to appear again. Experienced and knowledgeable leaders lead but also empower front line employees to solve problems immediately. Such an environment requires a culture of mutual respect and trust, open and honest communication, and synergistic and cooperating relationships of stakeholders” (p. 6).
Similarly, we can see that RFP refers here to the general atmosphere of the workplace. On the other hand, we have found definitions of RFP that are more directly focused on work aspects. Sartal et al.(2018) maintained that:
“Toyota reveals a particular form of respect, based more on practical than moral reasons, and its goals are to enhance workers’ involvement and their voluntary efforts and to draw out their full capacity” (p. 365).
Here, respect is not related to creating a generally friendly and open atmosphere, but more directly related to enhancing the workers’ capacity to work. Bodek’s (2008) definition is similar:
“You show people your respect by continually develop them, continually challenging them to learn to be better on the job, and allowing them to fully participate in identifying and solving problems” (p. 148).
In other words, the focus of these definitions is on workers’ abilities rather than on the actual individuals (Sartal et al., 2018). RFP is not a question of loving each other, as Sartal et al. (2018) put it, but of fostering workers’ skills and motivation to achieve their individual success and that of their firm. RFP in Toyota is based more on practical reasons and seeks to enhance workers’ involvement and their voluntary efforts and to draw out their full capacity. In the same vein, Coetzee et al. (2019b) argued that developing people into problem solvers and taking waste out of the system creates a leaner system. According to Coetzee et al. (2019a) and Emiliani (2009), the problem-solving process is the highest form of respect.
The above definitions are scattered examples of a topic that has not been systematically dealt with, although Coetzee et al. (2019a) engaged in a similar project to our own, going back to the sources and trying to find the true meaning of RFP through a systematic literature review. By reviewing key references, they found that RFP meant:
implementing teamwork as the foundation of the organization;
developing and challenging people;
motivating people;
developing people as problem-solvers;
assessing people’s safety in their daily tasks;
removing waste from people’s daily tasks; and
displaying people’s capabilities by entrusting them with greater responsibility and authority.
This definition of RFP is clearly centered on work-related aspects. Coetzee et al. (2019a) then took the step of making these findings into a framework that integrated the product value stream and the so-called people value stream. The product value stream, in Table 1, stems from Womack and Jones (2003), who developed a five-step process to improve organizations and achieve similar results as Toyota.
Womack and Jones’ (2003) five-step process may be the most used Lean tool (Liker and Hoseus, 2008). Value stream mapping involves following the product process from raw material to finished goods, documenting both value-added processes and wasted steps. Value stream mapping is useful to understand the product flows and identify the waste. The same methodology can be used studying people processes (Coetzee et al., 2019a; Liker and Hoseus, 2008). According to Coetzee et al. (2019a), co-workers feel that the people value stream actions are the key success actions in Lean. Lean implementation requires co-workers who are team-minded, competent, motivated, willing and able to identify and solve problems, aware of safety, efficient and accountable. Therefore, the people value stream needs to develop people to improve in those areas. The people value stream and the people are the most valuable assets of Lean and the rise or fall of the implementation (Coetzee et al., 2019a).
Coetzee et al. (2019a) combined Womack and Jones’ (2003) product value stream (Table 1) with the people value stream defined by the present authors (Figure 2). The traditional product value stream delivers a production system that highlights problems (bringing them to the surface) and the additional people value stream delivers people who can identify and solve these problems. The problem-solving process links the two value streams together and how it creates an environment of mutual trust, which leads to a leaner system (Coetzee et al., 2019a). Fujio Cho, Toyota’s former chairman, said: First we build people, then we build cars (Liker, 2004). According to Coetzee et al. (2019a), Cho’s statement is critical when implementing, transforming or improving Lean, which is why the improvement process (RFP framework) starts with the people value stream (Figure 2). Once the employees’ attributes have been developed (Steps 1 and 2), one can take the first step in the product value stream (Step 3) and define customer value and thereafter the other parts in the RFP framework.
The order of priority is chronological, starting with Steps 1, 2 and so on. In two places (Steps 4 and 5 and in Steps 9 and 10), both value streams work simultaneously. The framework shows that a culture similar to Toyota’s is created by involving all employees in the organization and giving them the opportunity to provide suggestions for improvement regarding their everyday work. The proposed framework also suggests how to practically work with RFP during Lean implementation by helping organizations have a more balanced focus between the Lean tools and techniques and the human side of Lean management. According to Coetzee et al. (2019a), when the product and value streams are connected and the problem-solving process is ongoing, it forms the true Toyota culture.
The work of Coetzee et al. (2019a) is highly valuable in its effort to go back to the sources, as well as to propose a practical framework that can be used by managers. However, we argue that, through the use of the hermeneutic method, we can propose a slightly different understanding of RFP that does not negate what Coetzee et al. (2019a) argued and instead provides more depth and can have additional practical implications.
What is the meaning of respect for people as defined by Toyota?
To understand the meaning of RFP, we provide some historical background below, to contextualize the principle.
Historical provenance of the respect for people principle
The term Lean was first introduced by Krafcik in 1988 (Chiarini et al., 2018; Yadav et al., 2017) but was popularized and spread by Womack et al. (1990), who used the term Lean production to describe a production system inspired by TPS. TPS was formed in 1926 when Toyoda Sakichi founded Toyoda Spinning and Weaving (Ohno, 1988). Ohno (1988), a former executive vice president of Toyota, worked in the Toyoda plant until 1943. In 1950 Ohno started to work at Toyota Motor Corporation (TMC) and began to develop TPS. The basis of TPS was the absolute elimination of waste, together with the equally important respect for humanity. Respect for humanity later became the base for RFP. TPS was established and based on two principles. The first is jidoka (which can be translated as automation with a human touch), which means that when a problem occurs, the equipment stops immediately, preventing defective products from being produced. The second is the Just-in-Time (JIT) concept, in which each process produces only what is needed for the next process in a continuous flow (Toyota Global Site, 2020b). Hayashi (2018), a former adviser to TMC who had 52 years of experience with the TPS, stated that the essence of TPS is jidoka and JIT, which in turn leads to genka teigen (cost reduction). When employees practice jidoka and JIT, human resources are developed. Thus, when the company rigorously follows jidoka and JIT, it will stimulate both cost reduction and human capital development.
In 2001 Toyota introduced the new Toyota Way, which can be considered an evolution of TPS (Liker and Hoseus, 2008). The Toyota Way 2001 was subsequently spread all over the world. As Toyota expanded its operations throughout the world, it encountered cultural challenges, as TPS is deeply rooted in Japanese culture. In the 1970s, Japanese Toyota managers Sugimori et al. (1977) pointed out the differences between Japanese and Western employees and their concept of work. The Japanese traits include group consciousness, a sense of equality, a desire to improve, centering their daily living around work and diligence born from a long story of homogeneous ethnicity, which could not be expected from employees in different countries.
Toyota’s principles before the Toyota Way 2001 were implicit. New employees gradually became accustomed to the company’s culture by means of the job exposure and training (Coetzee et al., 2019a). Toyota describes the improvement with written documents in its Code of Conduct (2018):
“We have established a corporate philosophy that has been passed down from generation to generation throughout the company and which has come to be known as the Guiding Principles at Toyota” (p. 3).
With the Toyota Way 2001, the company outlined its values in written form because:
“Such values and methods must be shared globally among us to realize the Guiding Principles and we are seeking to pass these on to future generations” (Toyota Code of Conduct, 2018, p. 3).
The model and The Toyota Way document was crafted while a Toyota senseis were teaching American managers about the concept (Liker and Hoseus, 2008), and it took almost 10 years of writing and rewriting before the Toyota Way was released (Coetzee et al., 2019a). The transformation from TPS to the Toyota Way 2001 involved more than written documents. TPS’s two objectives (Jidoka and JIT) were also improved and became continuous improvement (CI) and respect for people (RFP). There were also changes in connecting principles, as can be seen in Table 2.
What should be noted from this historical overview is that the RFP principle was introduced when Toyota was clarifying its way of work to employees in other countries. However, although the principle became explicit in 2001, RFP was like all the other principles that were implicit and used even before the Toyota Way. Sugimori et al. (1977) stated:
“[…] the authority and responsibility for running and improving the workshop have been delegated to the workers themselves, which is the most distinctive feature of Toyota’s respect for humans” (p. 559).
Definition of respect for people as Ningensei Sontyo
As noted in the previous section, RFP was used at Toyota before the Toyota Way 2001 but was made explicit to successfully communicate with stakeholders in other parts of the world. The Toyota Global Site (2020) explains respect as follows: “We respect others, make every effort to understand each other, take responsibility and do our best to build mutual trust” (Toyota Global Site, 2020a).
Here we will delve into the meaning of RFP if one studies the concept in Japanese. On the Toyota website, the original Japanese wording of the English term Respect for People was Ningensei Sontyo (⼈間性尊重). The word sontyo, used to signify respect, is one of 18 concepts within the Japanese language that are considered to correspond more or less to the English concept of respect (Muto, 2016). Given that there are a range of possible concepts, why is RFP called ningensei sontyo and not, for example, ningensei sonkei?
To understand the concept of sontyo, we explored the work of Muto (2016), who described the word respect from three different angles. The first is translated as sontyo (Muto, 2016, Li and Fischer, 2007), while the latter two correspond to sonkei:
Ought-respect refers to the kind of respect everyone deserves based on political, moral and legal considerations and applies to everyone. Ought-respect is tied to a rights-based moral principle and mandated by law, and it is not person- or relationship-specific. Rather than being a prototypical emotion, ought-respect is more of a reason-based social, moral and attitudinal construct. Respect for authority is ought-respect (sontyo).
Respect as an emotional attitude toward a certain person; for example, I have always respected Ms. A. (sonkei).
Respect as an emotional state, which means respect related to something someone does. Muto (2016) partially draws on Li and Fischer (2007), who discussed concepts of respect within the Chinese language from which parts of Japanese written language stem (sonkei).
Muto’s (2016) second and third categories are classified as affect-respect, an emotion that is mostly generated in a specific social context or relationship (Li and Fischer, 2007). This kind of respect occurs when an individual genuinely recognizes, acknowledges and admires another for his/her merit, achievement, moral qualities and status/position/role/power. People feel this kind of respect toward certain people without necessarily expecting them to extend the same kind of respect back to them. Affect-respect is not necessarily tied to a moral principle or mandated by law; people do not extend this kind of respect to everyone. They feel affect-respect only toward certain persons in a temporal sense. They respect when they recognize the good qualities of a person, but they also lose respect for a person they have previously admired if, for example, that person’s moral character becomes questionable later. Affect-respect can come and go and rise and fall as our appraisal of the person changes, as stated earlier.
Comparing this discussion with the meaning of respect in English, we can see that several meanings are conflated into the same term. In the Oxford-powered UK dictionary Lexico (2020), the word respect, as a verb, contains both ought-respect and affect-respect:
Verb (with object)
1. A feeling of deep admiration for someone or something elicited by their abilities, qualities, or achievements (she was respected by everyone she worked with).
1.1 Have due regard for (feelings, wishes, or rights) (I respected his views).
1.2 Avoid harming or interfering with
(it is incumbent upon all hill users to respect the environment).
1.3 Agree to recognize and abide by (a legal requirement)
(the crown and its ministers ought to respect the ordinary law).
The former definition is related to affect-respect, while the latter is related to ought-respect. In summary, the differences between the concepts of respect in English and in Japanese are that, in English, respect comprises both ought-respect and affect-respect.
What we can learn from this definitional exercise is that the respect that is called for in the RFP principle is related to ought-respect, a respect that is a basic form of due regard and is unrelated to the particular actions or achievements of individual employees.
Now let us turn to the concept of the human in the RFP principle. Toyota does not use (⼈間尊重) ningen sontyo, but rather ningensei sontyo (⼈間性尊重). In English, the former would be respect for humans/persons, while the latter, which Toyota uses, would be respect for humanity/personhood. According to Kuwabara (2017) and Fukui (2016), there is quite a clear interpretation of what the concept that Toyota uses does and does not mean. It does not mean respecting humans/people, but rather respecting the thinking power of people. Toyota’s Official Site (2020a) explains that RFP means more than respecting the thinking power; it is also about respecting people’s power and productive power. Thus, RFP is not about a fuzzy kind of respect; it is clearly directed to the productive and thinking powers of the people working at Toyota.
However, we are still quite close to the definitions that are already provided in the Lean literature: RFP as encouraging the implementation of teamwork as the foundation of the organization, developing and challenging people, motivating people, developing people as problem-solvers, assessing people’s safety in their daily tasks, removing waste from people’s daily tasks and displaying people’s capabilities by entrusting them with greater responsibility and authority (Coetzee et al., 2019a).
Respect for people within the context of monozukuri, hitozukuri and kotozukuri
Before continuing to dissect the principle of RFP, it is important to discuss the underlying philosophy of TPS. When explaining their production philosophy and backbone of the company, Toyota employs the concept of monozukuri (Liker and Hoseus, 2008; Toyota, 2012; Toyota Global Site, 2020c). At Toyota, monozukuri means “an all-encompassing passion for innovating and doing things well” (Liker and Convis, 2012, p. 229). While monozukuri can be simply translated into “making things” (Ballé et al., 2019), monozukuri connects to a long Japanese tradition and philosophy of creating quality products and services (Tiphtarajan, Lertrusdachakul and Mahatanankoon, 2019). This concept possesses a deeper meaning that aligns with craftsmanship or making things by hand, and it offers the idea of possessing the “spirit to produce excellent products and the ability to constantly improve a production system and process” (Smarandache, Christianto and Boyd, 2019, p. 498), as well as dedication and the striving for improvement (Kovacic, 2018).
Toyota connects monozukuri to hitozukuri (making people). What is often stated – for example on the Toyota Global Site (2020d) – is that monozukuri is hitozukuri. Hitozukuri refers to the process of cultivating a craftsman’s spirit (or human capital) through continuous learning, apprenticeship, mentoring and self-reflection (Tiphtarajan et al., 2019) or, in short, the cultivation of a quality person (Ballé et al., 2019; Tiphtarajan et al., 2019). According to Ballé et al. (2019), Toyota’s theory of hitozukuri, of how to develop people, is based on employees understanding the content of the job, being confident in their successes and keen to take on new challenges, offered a space to think and seeing themselves progress.
Ballé et al. (2019) have suggested that there is a third term related to hitozukuri and monozukuri, namely, kotozukuri. Kotozukuri brings together two different notions: the need for storytelling and narratives to keep everyone on the same track, and the managerial energy to make the story come to life. We interpret Ballé et al. (2019) to mean that these overall guiding stories, visions and fantasies are needed to get the employees on the right path and see that all the small improvement measures are connected to a grander story and purpose.
We have now turned to the underlying philosophy of monozukuri, hitozukuri and kotozukuri. One can connect monozukuri to the product value stream and hitozukuri to the people value stream, as discussed by Coetzee et al. (2019a, 2019b) and thereby understand the interconnections among the terms. The RFP principle is also understandable in relation to monozukuri and hitozukuri; that is, the connection to craftsmanship and the cultivation of a person to become a craftsperson. We believe that a potential way to go deeper still is to turn to the concept of takumi.
Respect for people as respect for takumi
In our quest to seek deeper meanings, we were inspired by Ohno (1988), who described respect for humanity rather than defining it. Ohno compared work with what can be called martial arts to highlight and respect the value of a worker and its knowledge. Ohno stated:
“In Japan competition is traditionally individual, as in sumo wrestling, kendo swordsmanship, and judo. In fact, we do not ‘compete’ in these activities but rather we ‘seek the way and study it’ devotedly. This approach has its analogy in the work arena, where the art of the individual craftsman is highly valued” (p. 23).
Ohno (1988) further accentuated the Japanese history and culture, saying that:
“If in the United States there is management magic, then in Japan, we call it in the Toyota Production System by ninjutsu [the art of invisibility (cf. the skills of ninja to be almost invisible)], a reflection of its Japanese character and culture” (p. 70).
Furthermore, Rother (2013) stated that it seems to be hard for the Toyota employees to explain the unique thoughts and routines at Toyota. It is just the normal way of work; it is within the Toyota culture. For example, asking someone what they did at work today would probably result in them describing the duties they performed. However, some things we do without realizing it, such as breathing, would probably not be included and can be an example of these indescribable acts at Toyota. A closer look shows that Lean is less about tools, method and principles than it is about procedures – mind and act patterns. By repeating them daily, we can get a desired result. In Japan this is called kata, which means a method or routine, a pattern, a standardized movement, a sequence of movements, or an exercise method or drill (Rother, 2013). The word kata originates from predetermined movement patterns within budo (martial arts), which are transferred from master to student over generations.
Furthermore, in recent promotional material, Toyota has advanced the concept of takumi – meaning the perfection of skill in craftsmanship – through a promotional video (Lexus Takumi, 2020). While it could have used the implicit, well-known and well-established concept of monozukuri to make sense of their work with Lexus, Toyota instead emphasizes this perfected form craftsmanship with the word takumi. The video featuring Lexus illustrates the survival of takumi despite the modernization of industry. In this video, it is said to take 60,000 hours to achieve takumi, through the mindful (kata-like) repetition of thinking and action. Whether it is the English 10,000 hours of practice or the 60,000 hours of takumi, we believe that the view of this perfected form of craftsmanship is central to Toyota. Very few texts have been written about takumi within the English-speaking literature on Toyota.
An exception is Takahashi and Lennerfors (2012), who connected the world of takumi that is sought after at Toyota with the martial arts mentioned by Ohno (1988). Takahashi and Lennerfors argued that, through their work practice, one could even argue that employees are on a quest to reach satori (enlightenment). According to the Japanese dictionary Kojien (cited in Takahashi and Lennerfors (2012), satoru (the verb related to satori) has three meanings:
to clearly understand the way of everything;
to surmise, or to sense; and
to leave the wanderings of the heart behind and realize the truth.
Similar to swordsmanship, the point is not only to be skillful but to grasp deeper meaning through practice. Although one could certainly problematize whether satori can be reached by building cars, the concept of takumi is widely present in Toyota’s training facilities, where it is explained how the mind, skills and body become one and is strengthened by the power to instruct or lead (Figure 3).
Takumi used to refer to woodworkers, but it now means people with excellent skills (Takahashi and Lennerfors, 2012). In its traditional sense, a dojo is a place to practice martial arts; at Toyota, a training-center is known as a dojo and the training is facilitated by a TPS expert, a sensei, a term that means both master and teacher (Liker and Convis, 2012). Reke et al. (2019) interviewed a Toyota veteran who said “TPS is a hard sell, it’s about getting people to take ownership in their work and then supporting them to successfully complete the work” (p.121). The sensei supports that ownership process, for example by providing practical exercises for trainees, involving them in improvement work, challenging the executives, making the trainees test their hypotheses by using the Plan, Do, Study, Act cycle and also pushing trainees to take the next step. In other words, “the role of sensei is to provide challenges, structured opportunities, and coaching, so that the student has an opportunity to learn by doing” (Liker and Convis, 2012, p 51).
We argue that these indications from Toyota’s promotional material, as well as its in-house operations, mean that Toyota works with an idea of promoting takumi. This, we claim, is the core meaning of the RFP principle – namely that it is not respect for any people but respect for craftspeople trying to strive for takumi. There is a possible counter-argument that Toyota does not mean what it says but rather tries to create legitimacy and gain respect from employees and other stakeholders. This is in line with an argument by Mehri (2006), who exposed the darker (in other words, more exploitative) side of Lean implementations, arguing that in such implementations the legitimate discourse of respect and quality is used, while, under the veneer, more respect is paid to cost-cutting and direct profits than to people. Establishing the factual correctness of such claims would require extensive empirical research, which is beyond the scope of the present paper.
To sum up, we have argued above that the notion of takumi is what brings together the connections between modern production systems and references to swordsmanship (Ohno, 1988), the use of the concept of dojo and sensei at Toyota (Takahashi and Lennerfors, 2012; Reke et al., 2019) and also the concept of kata, a repetitive form of training for reaching excellence (Rother, 2013).
How can respect for people be translated into other contexts?
In our review of Lean literature, we argued that there had been confusion regarding the concept of RFP. Lean implementers outside Japan know that it is important but have failed to implement it in practice. Would it be better to talk about respect for takumi as a key to Lean implementation? We believe that it could potentially lead to even more confusion, and perhaps exoticization about the core message of takumi. This is why we see this as an opportunity to revive a discussion about craftsmanship within Lean implementation literature.
Toyota promotes a philosophy of craftsmanship, and our interpretation is that RFP means respect for craftsmanship. But what is craftsmanship? Recently, there has been some focus on crafts within fields such as philosophy (Coeckelbergh, 2012, 2013, 2015, 2019), as well as management and organization studies (Mintzberg, 2009; Taylor et al., 2015; Bell and Willmott, 2020). For an overview of the concept of craft, we find philosopher Coeckelbergh’s conceptualization valuable (for example, Coeckelbergh, 2012, 2013, 2015, 2019). Coeckelbergh constructed an understanding of craft based on the works of Richard Sennett, Hubert Dreyfus, John Dewey, Aristotle, Alasdair MacIntyre and Albert Borgmann.
In the present paper, craftsmanship is conceived as skilled work that involves physical and bodily engagement with things, and the nature of this engagement is what leads to good quality. As such, craftsmanship implies practical knowledge: knowing-how, rather than knowing-that (Dreyfus and Dreyfus, 1991). Knowing-how is constructed as part of habits. Coeckelbergh (2012) maintained that, in our habits and skilled activities, we are in the world in a way that resembles breathing (cf. Rother, 2013). By engaging in skilled activities, a person is reconciled with tools and materials, and the inside and outside of the skilled activities are also merged. To understand Lean implementations, one must clearly understand what employees do in their particular habits. In the theories of craftsmanship, knowing-that (the knowledge of techniques, principles, codes and rules) is not enough; what is important is knowing how to do things well; in other words, developing good skills, habits and practical know-how. For novices, rules and guidelines can play a role, but people with more developed moral expertise rely on their phronesis – practical wisdom.
In craftsmanship, the means and the ends merge (Dreyfus and Dreyfus, 1991). It is not good craftsmanship if, say, one produces good results for the bottom line a particular year, but the process has been fraught by questionable practices, unethical relationships to colleagues or customers. However, the opposite is also true, that good craftsmanship is not about being completely ethical towards colleagues, customers and managers, if it comes at the price of failing to produce the desired end result. Furthermore, in good craftsmanship, one cannot easily separate technical and moral knowledge. The technical expertise of creative thinking, accurate skills and team-working skills is as important as the ethical aspects, namely, that the work cultivates the employee, his or her relationships to colleagues and manifests care for the industrial setting.
Indeed, care is a central part of the notion of craftsmanship. Dreyfus and Kelly (2011) suggested that by being involved in skilled activities, we can learn to care for things rather than treat them just as resources, such as merely seeing material as raw material, or a job simply as a way to make a living. Dreyfus and Kelly (2011) gave the example of a wheelwright who achieves a kind of intimacy with the wood and has a feeling of care and respect for it (Dreyfus and Kelly, 2011; Coeckelbergh, 2012). This is also present in Toyota manager Kikuo Suzumura’s saying: “don’t look with your eyes but with your feet, don’t think with your head but with your hands” (Hayashi, 2018).
The focus on care for materials, processes and people stands in contrast to the predominant understanding of Lean, where there is a dichotomy between the product value stream and the people value stream. The notion of craftsmanship situates the employee in the middle of relationships to people and objects that demand his or her care. The good should not be understood in a merely technical sense but also in an ethical sense. The craftsperson becomes a virtuous person through his or her work.
Coeckelbergh (2013) also argued that craft has a social dimension and that a craftsperson can only develop into a virtuous person within a community. Furthermore, the craft itself contributes to building communities and solidarity within them. Coeckelbergh (2012) drew on Crawford (2009) to argue for the social dimension of the craft – that the craft flourishes as a result of a common skilled activity, such as common problem solving.
While takumi can be hard to digest in non-Japanese contexts, we believe that we should take the concept of craftsmanship as a foundational idea in Lean implementation. Craftsmanship has a long tradition within Western contexts and some theorization, such as that of Coeckelbergh (2012), can be communicated as the core underlying value of Lean implementation.
Concluding discussion
The purpose of this paper was to achieve a better understanding of the Lean principle of RFP to facilitate Lean implementations. To do that, we have explored RFP through an interpretative, hermeneutic method that has involved studying the lean literature in English, original Japanese sources, as well as an inquiry into the meaning of concepts.
To summarize, we have made the following findings. First, the lack of RFP is seen as a major hindrance to successful Lean implementations outside Japan. However, the literature claiming that the lack of RFP is an obstacle contains a broad range of definitions of RFP. Also, despite the comprehensive approach of Coetzee et al. (2019a), we maintain that it is possible to gain a deeper understanding of the RFP principle. This led us to revisit the sources from Toyota and others close to the company. We note that the concept of respect is not of the emotional kind, but rather ought-respect; in other words, respect as due consideration. For some Lean implementers, this could be a novel contribution, as they might see respect as a combination of affect-respect and ought-respect.
We also understood that the concept of people in RFP corresponds to personhood/humanity (ningensei), which according to Toyota is about bringing out the capacity of thinking and producing in every human being. In our survey of the literature on monozukuri, hitozukuri and kotozukuri, we found that hitozukuri – the development of people – is deeply connected to monozukuri – the art of making things or craftsmanship – and that the RFP principle is related to hitozukuri. This message of definition can be seen as: Toyota does not just build cars. They build people. This is in line with the motto that “monozukuri is hitozukuri”, At the same time, RFP means enhancing workers’ involvement and their voluntary efforts and drawing out their full capacity. This message of a definition could be: Toyota build cars, using people.
Based on scattered remarks by Ohno (1988) as well as other scholars, we made the link between the notion of people in RFP and an understanding of takumi, a form of perfected craftsmanship which Toyota differentiates as something even better and more refined than the implicit, well-known and well-established monozukuri. We argued that this is the underlying understanding of the word people in RFP, namely, people striving for takumi. Given that there is no clear equivalent to takumi in English, we translated takumi back to English as a perfected form of craftsmanship and presented an understanding of a modern, Western conceptualization of craftsmanship. Consequently, we maintain that RFP should be interpreted as respect for craftsmanship – RFC. This understanding of RFC leads to new research avenues, both descriptive and analytical, which study how employees perceive that their craftsmanship changes from Lean implementations, and more normative, action-oriented projects that would try to implement Lean with the notion of craftsmanship in mind.
In terms of the practical implementations of RFC, we again agree with Van Assen (2018) that 80% of the effort needs to go to driving people change and the remaining 20% can focus on tools. Although we truly respect the work of Coetzee et al. (2019a), we feel that, in their aim to make the framework palatable to managers, they may have focused too much on the tools side of the people value stream. While this paper is not primarily meant to offer practical guidance, a first sketch of possible practical implications will be made here. Following the surveyed theories of craftsmanship, craftspeople perform skilled work that requires practical knowledge – know-how – which is strengthened through continuous habits (Dreyfus and Dreyfus, 1991). From this follows a first postulate, namely, that Lean implementations need to acknowledge that employees perform skilled work, and that such implementations should be based on an in-depth understanding of the skilled work performed by employees. One should not jump to conclusions regarding value and waste, but instead seek a deep understanding of the habits, routines, and know-how that employees engage in. This is not to romanticize the status quo but also not to too easily dive into a Lean implementation without understanding what important habits, routines and know-how can possibly be lost. One way to reach an understanding of this is to study work practices but also to involve the affected employees in a reflection and subsequent discussion about their skilled work, their know-how and their habits. Employees can then suggest how Lean principles and tools can be used to strengthen their skilled work.
Second, care is a central part of the notion of craftsmanship. The notion of craftsmanship situates the employee in the middle of relationships to people and objects that demand his or her care (for example, a wheelwright’s care for the wood and for his customer) how the wheel will be used, care for the profession of wheelwrights and its standards, care for the people working in his workshop, etc. (Dreyfus and Kelly, 2011; Coeckelbergh, 2012). The quality of the work in this complex system is based on the successful balancing of these different concerns. From this follows a second postulate, that Lean implementations need to be based on an understanding of existing care relationships and an understanding of how the Lean implementation might disrupt care relationships. Furthermore, Lean implementations should involve a discussion about how different values and interests are emphasized, such as an increasing focus on profitability, which might have a negative impact on other care relationships. For example, Coeckelbergh (2013) discussed nursing and argued that contextual demands in the form of demands of efficiency limit the possibility of engaging in nursing as a craft. It is important for organizations to provide the possibilities for craftsmanship and not undermine the foundation upon which excellence is built. Similar to the previous point, spaces for dialogue could be created for this purpose, conducive for discussions about care at work and the balancing of care relationships. This could also open up for a more nuanced discussion of waste and how some practices that do not at first sight seem to have a connection to profitability and quality might indeed be indirectly related.
Third, craft has a social dimension and that a craftsperson can only develop into a virtuous person in a community (Coeckelbergh, 2012; Crawford, 2009). Furthermore, the craft itself contributes to building communities and solidarity within them, at a workplace. From this follows a third postulate that Lean implementations need to be done with an understanding of the social dynamics of the workplace and how it relates to craftsmanship; in other words, how quality work builds communities and connections between employees. Lean implementations need to involve the employees that are subject to Lean. In the notion of craft, RFP means to promote a framework of innovation, inspiration and teamwork by building a culture of inquiry, questioning, improvement, proactive behavior, shared beliefs and values.
A final piece of practical advice comes from a combination of craftsmanship with the notion of kotozukuri (Ballé et al., 2019). An important purpose of the craftsmanship concept developed in our paper is to provide an overarching story of the work of the employees in the organization. We believe that craftsmanship as a notion is a way to increase the value of the work done by employees, and that there would be real effects if both employees and managers see the work being done in the organization as craft. With such a story in place, it would become clearer if the intended or ongoing Lean implementations indeed correspond to respecting craftsmanship, or if they are too focused on lean tools or have an overly narrow focus on cost reduction, without realizing the idea of genka teigen – that is, that cost reductions are achieved by developing people, or in our understanding, by a respect for craftsmanship.
Figures
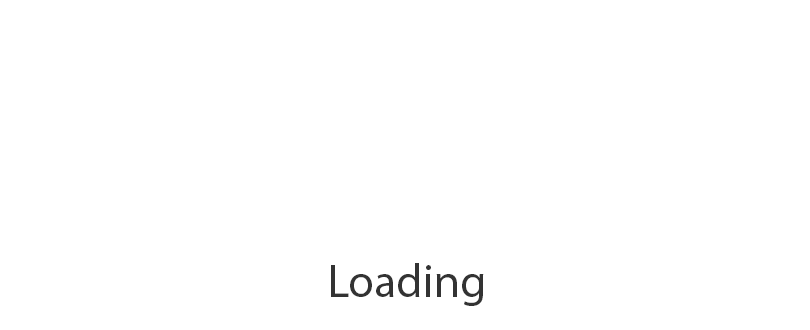
Figure 2.
RFP Framework developed by Coetzee et al. (2019a)
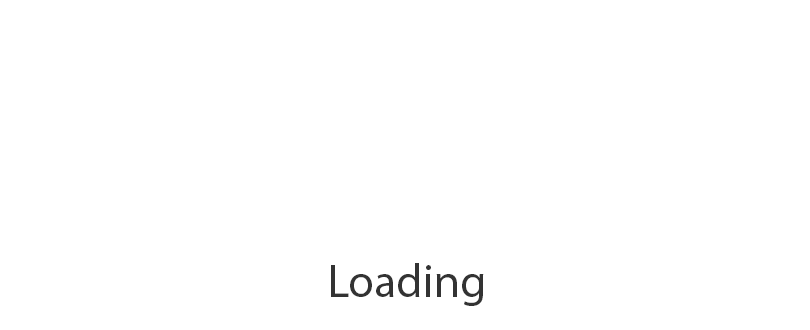
Figure 3.
The human resources model that Toyota aims for (Takahashi and Lennerfors, 2012)
Lean thinking according to Womack and Jones (2003)
1. Define customer value | Define value in terms of specific products and capability offered at specific prices to specific customers |
2. Identify the value stream | Identify the entire value stream for each product and remove all waste from the process |
3. Make it flow | Make the remaining value-creating steps flow by fighting against departmentalized batch thinking, and focusing on the product and its needs rather than the organization or equipment |
4. Pull back from customer | Do less forecasting and let the customer pull the product as it is needed, rather than pushing often unwanted products onto the customer |
5. Striving for excellence | There is no end to the process of reducing effort, time, space, cost, and mistakes while offering a product which is more what the customer wants |
The five-step Lean process is also called the product value stream
Compilation of principles and methods of TPS and the Toyota way 2001
Model | Principle | Method |
---|---|---|
Toyota Production System | Autonomation/Jidoka | • Stopping the line • Teamwork • Five Whys |
• Just-in-time (JIT) | •Takt-time and continuous flow • Kanban • Waste recognition and elimination |
|
Toyota Way 2001 | Continuous improvement (CI) | Challenge Kaizen Genchi Genbutsu |
Respect for people (RFP) |
• Respect “We respect others, make every effort to understand each other, take responsibility and do our best to build mutual trust.” (Toyota Global Site, 2020a) Teamwork “We stimulate personal and professional growth, share the opportunities of development and maximize individual and team performance.” (Toyota Global Site, 2020a) |
This paper focuses on the RFP principle, so only that principle and its methods are described in the table
Source: Inspired of Chiarini et al. (2018), Ohno (1988), Toyota Global site (2020a)
The result of the literature search in numbers
Article | Mention RfP |
Discuss RfP | Define RfP |
Lack of RfP |
Mention Respect | Mention People | Discuss Respect |
Discuss People |
Define Respect |
Define People |
Mention Culture |
---|---|---|---|---|---|---|---|---|---|---|---|
A) Yadav, Nepal, Rahaman, and Lal (2017) 227 | X | X | X | X | X | X | X | X | |||
A) Zhang et al. (2017) 230 | X | X | X | X | X | ||||||
A) Ingelsson, and Bäckström (2017) 237 |
X | X | X | ||||||||
B) Coetzee, Jonker, van Dyk, and van der Merwe (2019 b). (also found in A) 1 |
X | X | X | X | X | X | X | X | X | X | |
B) Ngadiman et al. (2019) (also found in A) 2 | X | X | X | X | |||||||
B) Hozak and Olsen (2019) (also found in A) 3 |
X | X | X | X | X | x | X | X | |||
B) Coetzee, Jonker, van Dyk, and van der Merwe (2019a). (also found in A) 4 |
X | X | X | X | X | X | X | X | X | ||
B) Chiarini et al. (2018) (also found in A) 5 |
X | X | X | X | X | X | |||||
B) Wilson, Jayamaha, and Frater (2018) (also found in A) 6 |
X | X | X | X | X | ||||||
B) Sartal, Martinez-Senra, and Cruz-Machado (2017) 7 |
X | X | X | X | X | ||||||
B) Gong, and Blijleven (2017) (also found in A) 8 |
X | X | X | X | |||||||
B) LeMahieu, Nordstrum, and Greco (2017) 9 |
X | X | |||||||||
B) Coetzee, van der Merve, and van Dyk (2016) 1) |
X | X | X | X | X | X | X | ||||
B) Gao, and Low (2015) 11 | X | X | X | X | |||||||
B) Halling (2014) 12 | X | X | X | ||||||||
B) Johnson, Patterson, and ÓConnell (2013) 13 |
X | X | X | ||||||||
B) Marksberry (2011) 16 | X | X | X | X | |||||||
B) Keif (2009) 17 | X | X | |||||||||
B) Oppenheim et al. (2010) 18 | X | X | X | X | X | X | |||||
B) Cooper (2008) 19 | X | X | X | X | |||||||
B) Hunter (2008) 20 | X | ||||||||||
B) Emiliani (2006) 21 | X | X | X | ||||||||
B) Hunter, Bullard, and Steele (2004) 22 |
X | ||||||||||
100% | 61% | 22% | 61% | 52% | 43% | 26% | 9% | 22% | 0 | 70% |
All 23 articles are represented in the table. The number after the authors is the number the article has in the search
Appendix
References
Van Assen, M., doi (2018), “Exploring the impact of higher management leadership styles in lean management”, Total Quality Management and Business Excellence, Vol. 29 Nos 11/12, pp. 1312-1341, doi: 10.1080/14783363.2016.1254543.
Ballé, M., Powell, D. and Yokosawa, K. (2019), “Monozukuri, hitozukuri, kotozukuri”, Planet Lean, available at: https://planet-lean.com/monozukuri-hitozuku ri-kotozukuri/ (accessed 2 November 2020).
Belhadi, A., Touriki, F.E. and Elfezazi, S. (2019), “Evaluation of critical success factors (CSFs) in lean implementation in SMEs using AHP. A case study”, International Journal of Lean Six Sigma, Vol. 10 No. 3, pp. 803-829, doi: 10.1108/IJLSS-12-2016-0078.
Bell, E. and Willmott, H. (2020), “Ethics, politics and embodied imagination in crafting scientific knowledge”, Human Relations, Vol. 73 No. 10, pp. 1-22, doi: 10.1177/0018726719876687.
Berger, P.L. and Luckmann, T. (1966), The Social Construction of Reality: A Treatise in the Sociology of Knowledge, Anchor Books, Garden City, New York, NY.
Bodek, N. (2008), “Leadership is critical to lean”, Manufacturing Engineering, Vol. 140 No. 3, pp. 145-155.
Bäckström, I. and Ingelsson, P. (2016), “Measuring appreciative inquiry, lean and perceived Co-worker health”, Quality Innovation Prosperity, Vol. 2 No. 20, pp. 105-118, doi: 10.12776/QIP.V20I2.744.
Chiarini, A., Baccarani, C. and Macherpa, V. (2018), “Lean production, Toyota production system and kaizen philosophy. A conceptual analysis from the perspective of Zen Buddhism”, The TQM Journal, Vol. 30 No. 4, pp. 425-438, doi: 10.1108/TQM-12-2017-0178.
Cochran, D., Schmidt, G., Oxtoby, J., Hensley, M. and Barnes, J. (2012), “Using collective system design to define and communicate organization goals and related solutions”, Journal of Enterprise Transformation, Vol. 7 Nos 1/2, doi: 10.1080/19488289.2017.1339746.
Coeckelbergh, M. (2012), “Technology as skill and activity: Revisiting the problem of alienation”, Research in Philosophy and Technology, Vol. 3 No. 16, pp. 209-230.
Coeckelbergh, M. (2013), “E-care as craftsmanship: virtuous work, skilled engagement, and information technology in health care?”, Medicine, Health Care and Philosophy, Vol. 16 No. 4, pp. 807-816.
Coeckelbergh, M. (2015), Environmental Skill, Motivation, Knowledge, and the Possibility of a Non-Romantic Environmental Ethics, Routledge, New York, NY.
Coeckelbergh, M. (2019), “Skillful coping with and through technologies”, AI and Society, Vol. 34 No. 2, pp. 269-287.
Coetzee, R., van Dyk, L. and van der Merve, K. (2019a), “Towards addressing respect for people during lean implementation”, International Journal of Lean Six Sigma, Vol. 10 No. 3, pp. 830-854, doi: 10.1108/IJLSS-07-2017-0081.
Coetzee, R., Jonker, C., van Dyk, L. and van der Merve, K. (2019b), “The South African perspective on the lean manufacturing respect for people principles”, SA Journal of Industrial Psychology, Vol. 45, pp. 1-11, doi: 10.4102/sajip.v45i0.1613.
Crawford, M.B. (2009), Shop Class as Soulcraft: An Inquiry into the Value of Work, Penguin Press, New York, NY.
Dreyfus, H.L. and Dreyfus, S.E. (1991), “Towards a phenomenology of ethical expertise”, Human Studies, Vol. 14 No. 4, pp. 229-250.
Dreyfus, H. and Kelly, S.D. (2011), “All things shining”, Reading the Western Classics to Find Meaning in a Secular Age, Free Press, New York, NY.
Emiliani, M.L. (2009), “The equally important ‘respect for people’ principle”, available at: www.researchgate.net/profile/Ml_Emiliani/publication/265985726_The_Equally_Important_Respect_for_People_Principle/links/552594b10cf24b822b40560e.pdf,20-03-17
Foley, K. and Zahner, T. (2009), Creating and Managing the Sustainable Organization. The Stakeholder Way, SAI Global Limited, Sydney.
Fukui, T. (2016), “当たり前を実現する!トヨタのグローバル人材育成”, available at: https://globis.jp/article/4115,20-06-13 (accessed 11 April 2016).
Hayashi, N. (2018), “Toyota production system and the roots of lean”, available at: https://vimeo.com/300443389 (accessed 2 November 2020).
Kusy, M., Diamond, S. and Vrchota, S. (2015), “Real-Time culture change improves lean success: Sequenced culture change gets failing grades”, The Journal of Medical Practice Management, Vol. 1 No. 31, pp. 29-33.
Kuwabara, T. (2017), “人を切らないトヨタの家訓「金を使わず知恵を出せ”, President, available at: https://president.jp/articles/-/21438
Lexus Takumi (2020), available at: www.facebook.com/watch/?v=660104177760518
2020), available at: www.lexico.com/definition/respectLexico.
Liker, J.K. (2004), The Toyota Way. 14 Management Principles from the World’s Greatest Manufacturer, McGraw-Hill, New York, NY.
Liker, J. and Convis, G.L. (2012), The Toyota Way to Lean Leadership. Achieving and Sustaining Excellence through Leadership Development, McGraw-Hill, New York, NY.
Liker, J.K. and Hoseus, M. (2008), Toyota Culture. The Heart and Soul of the Toyota Way, McGraw-Hill, New York, NY.
Loh, K.L. and Yusof, S.M. (2020), “Blue ocean leadership activities improve firm performance”, International Journal of Lean Six Sigma, Vol. 11 No. 2, p. 359375, doi: 10.1108/IJLSS-09-2018-0102.
Marksberry, P. (2011), “The Toyota way – a quantitative approach”, International Journal of Lean Six Sigma, Vol. 2 No. 2, pp. 132-150, doi: 10.1108/20401461111135028.
Mehri, D. (2006), “The darker side of lean: an insider’s perspective on the realities of the toyota production system”, Academy of Management Perspectives, Vol. 20 No. 2, pp. 21-42.
Mintzberg, H. (2009), Managing, Berrett-Koehler, San Francisco.
Muto, S. (2016), “The hierarchical semantic structure of respect-related emotions in modern Japanese people”, The Japanese Journal of Psychology, Vol. 87 No. 1, pp. 95-101, doi: 10.4992/jjpsy.87.15304.
Ohno, T. (1988), Toyota Production System. Beyond Large-Scale Production, Taylor and Francis Group, New York, NY.
Oppenheim, B., Murman, E. and Secor, D. (2009), Lean Enablers for Systems Engineering, Wiley InterScience, doi: 10.1002/sys.20161.
Prasad, A. and Prasad, P. (2002), “The coming of age of interpretive organizational research”, Organizational Research Methods, Vol. 5 No. 1, pp. 4-11.
Reke, E., Powell, D., Olivencia, S., Coignet, P., Chartier, N. and Ballé, M. (2019), “Recapturing the spirit of lean: the role of the sensei in developing lean leaders”, Proceedings of the 6th European Lean Educator Conference, pp. 117-125.
Rother, M. (2013), Toyota Kata. Lärande Ledarskap, Varje Dag [Toyota Kata. Managing People for Improvement, Adaptiveness], Liber AB, Stockholm.
Rother, M. and Arbor, A. (2014), “About the toyota kata research”, available at: www.researchgate.net/publication/283638261_About_the_Toyota_Kata_Research
Sartal, A., Martinez-Senra, A. and Cruz-Machado, V. (2018), “Are all lean principles equally eco-friendly? A panel data study”, Journal of Cleaner Production, Vol. 177, pp. 362-370, doi: 10.1016/j.jclepro.2017.12.190.
Smarandache, F., Christianto, V. and Boyd, R.N. (2019), “How to balance intuitive and analytical functions of brain: a neutrosophic way of scientific discovery process”, EC Neurology, Vol. 11 No. 7, pp. 495-499.
Sugimori, Y., Kusunoki, K., Cho, F. and Uschikawa, S. (1977), “Toyota production system and kanban system. Materialization of just-in-time and respect-for-human system”, International Journal of Production Research, Vol. 15 No. 6, pp. 553-564.
Takahashi, M. and Lennerfors, T.T. (2012), “From mieruka to satoruka”, Business Review, Meiji University, Vol. 59 Nos 3/4, pp. 1-9.
Taylor, S.S., Ladkin, D. and Statler, M. (2015), “Caring orientations: the normative foundations of the craft of management”, Journal of Business Ethics, Vol. 128 No. 3, pp. 575-584.
Tiphtarajan, K., Lertrusdachakul, T. and Mahatanankoon, P. (2019), “Redefining ‘monozukuri’ in the context of information technology education”, Proceedings of the EDSIG Conference, available at: http://proc.iscap.info/2019/pdf/4973.pdf
Toyota (2012), “Detailed explanation of human Capital development”, available at: www.toyota.co.jp/jpn/company/history/75years/data/company_information/personnel/personnel-related_development/explanation.html
Toyota Global Site (2020a), available at: https://global.toyota/en/company/vision-and-philosophy/toyotaway_code-of-conduct/2020-06-08
Toyota Global Site (2020b), available at: https://toyotatimes.jp/en/insidetoyota/091.html
Toyota Global Site (2020c), available at: https://global.toyota/en/company/vision-and-philosophy/global-vision/2020-11-05
Toyota Global Site (2020d), available at: https://toyotatimes.jp/en/insidetoyota/093.html
Traylor, G. (2011), Lean Interacts with the Oil, Gas Industry. Exploration and Production, Hart Publications, Houston.
Womack, J.P. (2008), “Respect for people”, BP Trends, available at: www.bptrends.com/publicationfiles/THREE%2002-08-ART-Respect%20for%20People-Womack-final.doc.pdf
Womack, J.P. and Jones, D.T. (2003), Lean Thinking: banish Waste and Create Wealth in Your Corporation, Free Press Business, London.
Womack, J.P., Jones, D.T. and Roos, D. (1990), The Machine That Changed the World, the History of Lean Production, Rawsson Associates, New York, NY.
Yadav, O., Nepal, B., Rahaman, M. and Lal, V. (2017), “Lean implementation and organizational transformation: a literature review”, Engineering Management Journal, Vol. 29 No. 1, pp. 2-16.doi, doi: 10.1080/10429247.2016.1263914.
Further reading
Li, J. and Ficher, K. (2007), “Respect as a positive self-conscious emotion in European, Americans and Chinese”, in Tracy, J.L., Robins, R.W. and Tangney, J.P. (Eds), The Self-Conscious Emotions: Theory and Research, Guilford, New York, NY.
Toyota Code of Conducts (2018), available at: https://global.toyota/pages/global_toyota/company/vision-and-philosophy/code_of_conduct_001_en.pdf